Battery Manufacturing with 3D Printing and Advanced Materials
The rapidly evolving and changing technological landscape today has led to an increasing interest in and demand for higher-quality products. One of the technologies most affected by this environment and forced to continuously develop is electrochemical energy storage (EES) systems. Small-scale electronic devices that have become part of everyday life, such as mobile phones, smartwatches, and laptops, as well as large-scale electronic systems like electric vehicles and large-scale energy storage systems, all benefit from electrochemical energy storage (EES) systems. While this energy storage technology is often sufficient for the needs of these devices, it presents certain limitations in specific applications of some electronic systems.
Let’s examine together the study titled “3D Printing Technology for Rechargeable Li/Na-Ion Batteries,” published in the Journal of Energy Chemistry, which discusses these limitations and explores the applications of 3D printing technology in lithium-ion and sodium-ion battery manufacturing, one of the next-generation battery production techniques.
According to the study, these limitations stem from two main factors. The first is that traditional manufacturing methods do not fully meet the criteria of power density, safety, and cost for complex EES structures. The second limitation is that industrial applications capable of ensuring high battery performance in these EES systems have not yet provided sufficiently consistent solutions.
Introduction to Lithium-Ion (LIB) and Sodium-Ion (SIB) Batteries
Among today’s rechargeable batteries, lithium-ion batteries (LIBs) and sodium-ion batteries (SIBs) stand out as the best-performing and most widely adopted energy storage solutions. Both battery types operate on similar principles, and due to their shared energy storage mechanisms, similar design strategies can be applied to both. Because of these similarities, research into performance improvements using new manufacturing techniques can be conducted in parallel for both battery types.
LIBs and SIBs produced using traditional manufacturing methods feature a two-dimensional (2D) electrode structure. However, this 2D electrode structure leads to certain drawbacks, such as reduced porosity, negatively affecting electron transport, and increasing electrical resistance, which ultimately degrades overall performance.
The transition from two-dimensional to three-dimensional (3D) structures offers several advantages, including the formation of a well-organized porous structure, which has the potential to increase both energy and power density. Additionally, it shortens the transport distance for ions and electrons, thereby enhancing power density. While some manufacturing techniques have been developed to produce 3D-structured batteries, they are not yet commercially viable for large-scale production.
The Role of 3D Printing in Energy Storage Systems
As an additive manufacturing technology, 3D printing enables the rapid production of complex shapes without requiring molds, making it an efficient alternative to traditional manufacturing methods, especially subtractive manufacturing techniques. 3D printing constructs the final 3D structure by layering synthetic inks according to a pre-programmed design developed by advanced software.
Contributions of 3D Printing Technology to Battery Manufacturing
The study highlights that in recent years, 3D printing technology has been integrated into the research and development processes of energy storage and enhancement devices, yielding positive results.
The advantages of using 3D printing technology in energy storage devices include:
- The ability to produce customized and geometrically complex structures.
- The capability to create well-ordered hierarchical porous structures for electrodes used in device construction.
- Improving the conductivity of solid electrodes and optimizing diffusion distances.
- Reducing manufacturing costs by minimizing material waste in production processes.
- Enabling the integrated production of energy storage devices, eliminating the need for additional assembly steps and thus saving time.
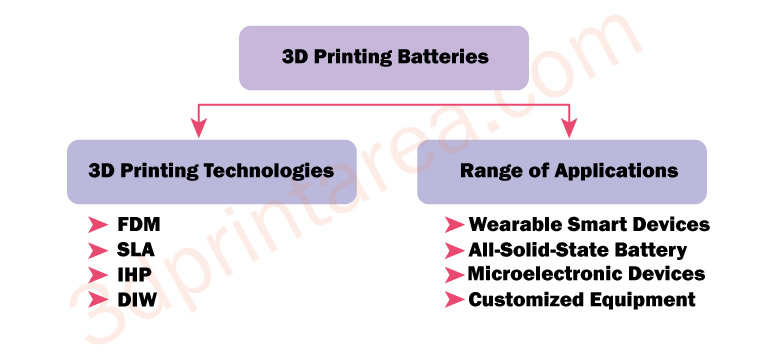
Anode Materials Produced with 3D Printing
The anode section of a battery is one of the most critical components affecting the overall energy density and performance of the battery. In energy storage systems, the conductivity, porosity, and electrochemical stability of the anode directly influence the battery’s overall performance. With the introduction of 3D printing technology in battery manufacturing, complex porous structures and enhanced ion transport in anodes can now be achieved more efficiently. These technological advancements offer significant advantages, particularly for lithium-ion (LIB) and sodium-ion (SIB) batteries.
Anodes produced using 3D printing technology are generally classified into four categories based on their reaction mechanisms:
Intercalation Reaction Anodes: These anodes feature materials such as graphite, amorphous carbon, and MXene, offering a stable cycle life due to their low volume expansion. With 3D printing, porous and highly conductive networks can be created, enhancing capacity and power density.
Alloying Reaction Anodes: Materials such as silicon, antimony, and bismuth undergo multi-electron alloying reactions with lithium or sodium. While these materials exhibit high theoretical capacities, significant volume expansion presents a challenge. 3D printing addresses this issue by forming flexible and porous structures, preventing material cracking and improving electrode stability.
Conversion Reaction Anodes: These anodes contain metal oxide, sulfide, or selenide-based materials. Similar to alloying reaction anodes, volume expansion is a major challenge. However, porous or carbon-coated structures created through 3D printing help mitigate the effects of volume expansion, making the process more tolerable.
Metal Anodes: Anodes in this category, particularly those containing lithium and sodium metals, offer high theoretical capacities but pose risks such as dendrite formation and unwanted side reactions with electrolytes. 3D printing technology plays a crucial role in mitigating these risks by creating porous metal scaffolds that prevent dendrite formation.
Future Outlook
In summary, 3D printing technology provides innovative solutions to key challenges in anode materials, such as volume expansion, low conductivity, and porosity issues. Various materials, including amorphous carbon, graphene, MXene, and metal-based compounds, can be transformed into high-performance anode systems through 3D printing. From a commercialization perspective, as industrial-scale, high-resolution, and rapid production techniques continue to evolve alongside material optimization, the development of higher energy density and longer-lasting batteries is expected in the coming years.
References
Chaudhary, A., Gustafson, D., & Mathys, A. (2018). Multi-indicator sustainability assessment of global food systems. Nature Communications, 9, 848. https://doi.org/10.1038/s41467-018-03308-7