Vat Photopolymerization Warpage Correction Delivers a Leap in Print Accuracy 🚀
Vat photopolymerization warpage correction is flipping the script on dimensional accuracy for intricate polymer prints. By evening out the light dose that each layer absorbs during curing, the method chops down curl distortion, sharpens measurement consistency, and turns polymer characterization into a far more trustworthy exercise.
🔍 What Exactly Causes Warpage in Vat Photopolymerization 3D Printing?
Layer-by-Layer Over-Curing: In bottom-up digital light processing (DLP), the early layers get blasted with photons again and again, soaking up extra energy and hardening more than the layers laid down later.
Uneven Shrinkage: That imbalance in cross-link density breeds internal stress; skinny or long, flat parts show the worst bending.
Print Accuracy Fallout: Curling of only a few degrees can upset optical tolerances in contact lenses or undermine foldable structures.
⚙️ Vat Photopolymerization Warpage Correction: Equalizing Light Energy Across Layers
Recent peer-reviewed studies propose a disarmingly straightforward fix: stretch the exposure of the very last layer so every slice soaks up the same total light energy — an adjustment mapped out by a tweaked Beer–Lambert equation.
Key Step – Why It Works
Measure unit absorbance with a quick curing-depth test: Turns Beer–Lambert theory into numbers the printer understands.
Calculate cumulative energy per layer: Custom scripts (think MATLAB) add up the stacked exposures.
Add one “extended-cure” layer: Levels total energy without touching the hardware.
The payoff? Warpage angle plummeted by 93 % for slender 0.5 mm specimens printed at 25 µm, diving from 31.3° to barely 2°.
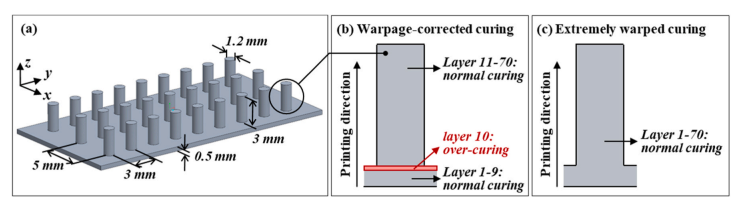
🧪 Dynamic Mechanical Analysis (DMA) Proves the Fix
Dynamic mechanical analysis (DMA) in three-point bending confirmed the turnaround: straightened samples showed roughly 5 % tighter deviations in flexural modulus than their warped twins. Because they sit flat, baseline misalignment disappears, giving engineers strength numbers they can finally trust when qualifying fresh resins or composite blends.
Bottom line: labs can read their DMA charts with confidence, free from the sneaky distortions that hidden curvature once introduced.
📊 Practical Guidelines for Resin Developers & Print Operators
Kick off with a 10-minute working-curve experiment to snag the unit absorbance (a) and the resin’s threshold exposure time.
Lock in an over-cure ratio of about two for the standard layers; then plug the numbers into E = t · e^(–a h) to work out the extra light dose the final layer still needs.
Give that extended-cure boost only to the bottom substrate slice; any pillars or micro-features printed on top stick with the usual exposure so their crisp edges stay razor-sharp.
Follow up in ImageJ—if your warp angle stays under 2° on thin parts, you’re in the clear.
Document every setting inside the slicer profile so anyone on the shop floor can hit repeat without guessing.
🚀 Why This Matters for Beginners, Hobbyists & Professional Engineers
Audience | Immediate Benefit |
---|---|
Beginners | Fewer failed prints and easier part removal—no more baffling curl-ups |
Hobbyists | Confidently crank out long, flat cosplay or RC parts minus the messy brims |
Professionals | Speedier material qualification, less scrap, and tighter tolerances for medical or aerospace fixtures |
🌐 Future Horizons: Beyond Curl-Free Parts
Adaptive Exposure Maps: Firmware that auto-calculates layer-by-layer light doses on the fly.
Real-Time Photodiodes: Closed-loop sensors verify every photon actually lands where it should.
Multi-Material VP: Blend elastomers with rigid resins without brewing up inter-layer stress.
As these upgrades arrive, warpage-correction know-how will become the backbone of everything from microfluidic chips to giant composite molds.
References (APA)
Lee, T., Ng, C. S., & Su, P.-C. (2025). Warpage correction for vat photopolymerization 3D printing. Additive Manufacturing, 102, 104740. Elsevier.
Advances in vat photopolymerization: early-career researchers. (2025). Royal Society of Chemistry.
How to improve the curing ability during the vat photopolymerization of ceramics. (2024). Materials. MDPI.
Effect of printing parameters on mechanical properties and warpage in PEEK parts. (2024). Manufacturing Processes. MDPI.