Vacuum-Assisted Extrusion 3D Printing: Revolutionary Void-Free Polymer Parts
Vacuum-Assisted Extrusion 3D Printing is an advanced approach that sucks hidden air and moisture out of large polymer builds while the material is still molten, wiping away the voids that normally sabotage big-format parts. Researchers at Oak Ridge National Laboratory (ORNL) recently proved that folding a compact vacuum chamber into the extrusion head can chop porosity by a hefty 75 percent. With those micro-pockets gone, prints roll off the bed measurably tougher and far more dependable than anything a standard nozzle can offer.
Vacuum-Assisted Extrusion 3D Printing: A New Frontier in Additive Manufacturing
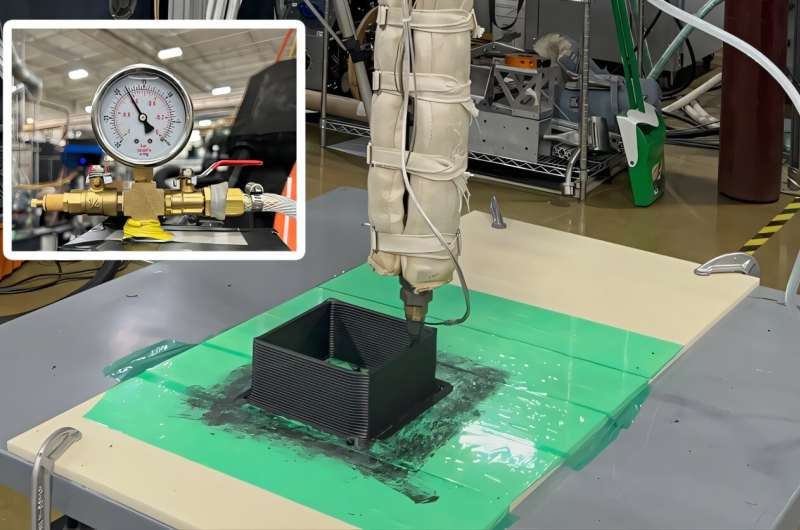
Image: A 3D-printing nozzle wrapped in insulation extrudes a composite polymer cube (foreground) while a close-up of a vacuum gauge (inset) shows the pressure applied. This vacuum-assisted extrusion 3d printing setup significantly cuts internal porosity in printed parts. (Credit: Vipin Kumar/ORNL)
In day-to-day terms, a part that once hid countless pin-sized gaps now emerges almost seamless; residual porosity often drops below 2 percent, even when the job involves notoriously tricky, fiber-reinforced thermoplastics. That near-solid density translates into higher load-bearing capacity, greater impact resilience, and a fatigue life long enough to handle real-world abuse—qualities that make the difference between a showpiece and a mission-ready component.
ORNL hails this steep drop in porosity as a “significant leap forward” for large-format additive manufacturing (LFAM), where meter-scale jigs or molds are printed in hours instead of weeks. Because those hulking parts must endure brutal clamping forces and shop-floor knocks, a single hidden void can spell early failure. With the vacuum now in play, LFAM customers can expect print-ready tooling that shrugs off higher torque, tighter tolerances, and longer production runs without cracking.
That promise hasn’t gone unnoticed. Stakeholders across aerospace, automotive, and defense—industries that pour fortunes into oversize fixtures—are already eyeing the technology to streamline production and shave weight from end-use parts. A process that once felt risky for mission-critical jobs now looks robust enough to clear the toughest qualification gates. Expect momentum to build as vacuum-equipped printers roll onto factory floors.
🚀 Up to 75 % fewer voids: Vacuum-assisted extrusion 3d printing carves away as much as three-quarters of the pores found in conventional prints, yielding parts that are almost seamless.
💪 Stronger polymers: With defects stripped out, the polymer matrix keeps its integrity, granting prints markedly higher toughness, stiffness, and fatigue resistance.
🌐 Industrial-scale impact: Tailor-made for large-format systems, the technique helps aerospace, automotive, and defense manufacturers hit demanding specs with less post-processing and re-work.
🛠️ How the Vacuum-Assisted System Works
The whole trick hinges on a deceptively simple upgrade: a vacuum-sealed hopper fixed to the filament feed. Before a single pellet meets the hot end, a pump draws out every whisper of moisture and air hiding between those particles. Carbon- or glass-filled composites usually smuggle in swarms of tiny bubbles during extrusion, yet this pre-degassing step lets the printer lay down layers that are markedly denser and more uniform.
During printing, the vacuum line never slows the show; material still streams into the nozzle without skipping a beat—just minus the trapped gases. ORNL’s team was pleasantly surprised to see the approach hold steady across wildly different fiber loadings, producing the same ultra-low porosity with carbon-reinforced compounds. In several trials, internal voids slipped below 2 percent, a feat conventional large-format machines can only envy.
Lead engineer Vipin Kumar puts it bluntly: “We’re conquering porosity and opening the door to tougher composites.” By essentially pre-conditioning the plastic, every layer fuses more completely, wiping out the “tiny chips in glass” defects that normally invite stress fractures. Printed brackets, molds, and fixtures therefore behave far more like traditionally machined parts when you push them to their limits.
🔎 Strength & Reliability: Void-Free Benefits for Polymers
Cutting pores from 3D-printed polymers pays off in a big way. FDM-style processes naturally trap voids as the material heats and cools, and every one of those gaps is a crack waiting to happen. Strip them out, and toughness, stiffness, and overall load-bearing muscle climb sharply.
Out on the test bench, vacuum-built samples handle stress with uncanny consistency. Where ordinary prints give up early, their void-free cousins boast higher tensile strength, shrug off impacts, and breeze through fatigue cycles. ORNL’s side-by-side trials showed vacuum-assisted parts enduring heavier loads than identical pieces printed the old way—a make-or-break distinction in safety-critical settings.
🔍 Reduced defect sites: With internal voids pushed to almost zero, stress concentrators virtually vanish—sidestepping the performance drop that microscopic pores usually cause.
🛡️ Enhanced durability: Minus the weak spots, printed tools and fixtures shrug off heavy loads, vibration, and heat swings without cracking—lab tests back it up.
🏆 Failure resistance: Vacuum-extruded parts prove far harder to break in mission-critical roles—think aerospace jigs or automotive fixtures—because they’re free of hidden flaws.
🚀 Vacuum-Assisted Extrusion 3D Printing: Applications & Industry Impact
Aerospace giants, automotive powerhouses, and any shop that leans on large-format 3D printing can finally consider printing jigs, molds, or oversized parts that clear the same brutal strength checks as their machined cousins. Because the vacuum retrofit bolts straight onto today’s LFAM hardware, nobody needs to spring for an all-new printer—just slip the degassing unit onto the hopper, and you’re off to the races. Interesting Engineering highlights how this drop-in upgrade “can be seamlessly integrated into existing LFAM workflows,” instantly tightening part quality across aerospace, automotive, and defense floors.
Knocking porosity out of fiber-reinforced composites also removes one of the last excuses engineers have for steering clear of production-scale printing. Purging voids addresses one of the final technical hurdles that has kept additive locked in prototyping. Put simply, fewer hidden flaws mean shops waste less time on reprints and QA failures, trimming costs while boosting confidence in every print that rolls off the bed.
🔮 Looking Ahead: Continuous Extrusion and the Road to Scale
ORNL’s team is already sketching the sequel: a patent-pending, real-time vacuum system that degasses filament on the fly, keeping the print head humming at full industrial speed. If they nail the design, factories could churn out void-free components 24/7 without a pause for batch conditioning.
In the nearer term, expect a wave of pilot projects as filament suppliers, printer OEMs, and service bureaus scramble to bundle “void-free” badges with their next product lines. Everyone in the additive ecosystem wants a slice of that reliability bump—and the market pull that comes with it.
Beyond polymers, the concept could spark spin-off tricks for powder-bed metals or resin systems—imagine vacuum-conditioned powders or bubble-free vats that deliver equally pristine layers. Each tweak chips away at the nagging weaknesses that still shadow additive manufacturing.
Zooming out, the bigger story is what happens when hidden voids stop dictating design limits. Engineers will be free to push build envelopes wider and geometries wilder, confident their printed parts won’t betray them under load. That shift could usher in an era where void-free, failure-resistant 3D printing is the rule, not the rare exception—a future where additive finally plays on equal footing with traditional manufacturing in both scale and strength.
References
ScienceDaily. Global science news platform.
PubMed Central. Open-access biomedical archive.
Oak Ridge National Laboratory. U.S. Department of Energy lab.
Interesting Engineering. Engineering & tech news site.