3D Printing and Additive Manufacturing Standards: An In-Depth Guide
3D Printing and Additive Manufacturing Standards ensure engineers can turn a digital design into a physical object with consistency and safety. Working layer-by-layer, the technology has transformed everything from rapid prototyping to full-scale production. Even heavyweight sectors such as aerospace, healthcare, and automotive are adopting AM at break-neck speed. With that rise comes a sharper focus on standards: they keep every build consistent, safe, and high-quality. In safety-critical fields, regulators (think civil-aviation authorities) demand that AM parts clear specific tests and meet iron-clad criteria. Thanks to standards, different manufacturers and users speak the same language; terms, measurements, and acceptance limits line up on common ground.
Most of that standard-setting effort is steered by ISO (International Organization for Standardization) and ASTM International. ISO’s TC 261 committee and ASTM’s F42 committee have, since the early 2010s, co-authored joint, global standards. The result is a family of dual-branded ISO/ASTM documents — the 52900 series is the poster child. In Europe, CEN/TC 438 fast-tracks those texts into EN standards, while national bodies such as DIN (Germany) and BSI (UK) adopt them at home. DIN’s own guidance — for instance DIN SPEC 17071 on quality management — has even paved the way for future international rules. In short, AM now enjoys a tightly woven, worldwide standards web. In this guide we’ll walk through the key ISO and ASTM standards, step-by-step along the AM workflow, unpacking what each one covers, how it’s applied, and why it matters on the shop floor.
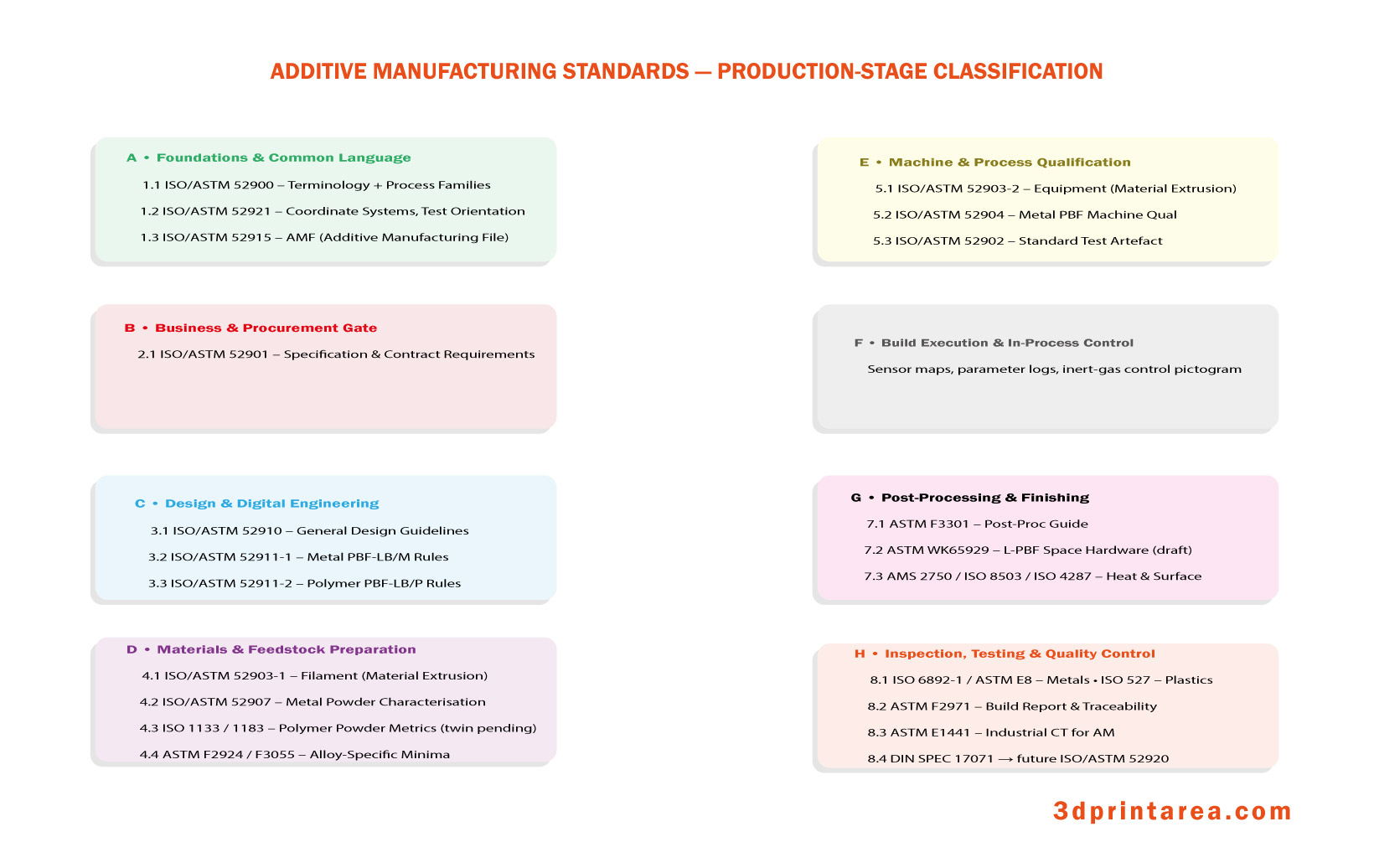
Standards on Terminology and General Principles
Because AM evolves at warp speed, forging a shared vocabulary is mission-critical. ISO/ASTM 52900, first published in 2015 and updated in 2021, does exactly that. It defines the seven core AM process families — powder bed fusion (PBF), material extrusion, material jetting, binder jetting, sheet lamination, directed energy deposition, and vat photopolymerization — plus everyday acronyms and machine parts. When someone says “PBF,” everyone pictures the same laser-sintering scene. The standard also locks in frequently used terms for AM machines and materials, ensuring that technical docs and vendor emails stay crystal-clear.
Another pillar is ISO/ASTM 52921:2013, covering coordinate systems and test terminology. It provides a single reference for build orientation on the print bed, axis labels (X, Y, Z), and build direction. Reporting a tensile coupon as printed “upright in Z” versus “flat in X-Y” is now unambiguous — vital, because AM part properties change with orientation. With 52921, labs from Tokyo to Toronto record test results with the same coordinate language.
Next comes ISO/ASTM 52901:2017 — essentially a contract template for buying AM parts. It lists everything customer and producer must lock down before hitting “print”: order data, CAD files or drawings, feedstock specs, target tolerances, required inspections, and acceptance criteria. Using 52901 up front cements quality assurance across the supply chain; both sides know the score from day one.
Data formats matter, too. The venerable STL mesh omits color, material, and internal structures. Enter ISO/ASTM 52915:2020 and its Additive Manufacturing File Format (AMF) — an XML schema that stores geometry plus color, material type, and even complex lattice fills. Need to print a copper insert or a porous core? AMF records it, and different slicers can swap files without a hiccup. Yes, industry also eyes 3MF, but 52915 remains the globally endorsed baseline for long-term data exchange.
Material and Feedstock Standards
AM success rides on the quality and suitability of its feedstock — be it filament, powder, resin, or wire. Because each AM process uses a different feed form, the standards are process-specific.
For material extrusion machines (your everyday FDM printers), the benchmark is ISO/ASTM 52903-1:2020. It spells out filament requirements: diameter tolerance, purity, moisture, melt behavior, and more. Vendors can certify that a PLA or ABS spool meets those numbers, and buyers can compare apples to apples. Its twin, 52903-2:2020, covers equipment basics — drive gears, nozzle specs, temperature control accuracy — to keep print quality steady.
In powder bed fusion, feedstock is fine powder. Both polymer powders (e.g., PA-12 for SLS) and metal powders (e.g., stainless steel or titanium for DMLS/SLM) are used. ISO/ASTM 52907:2019 is the heavy hitter for metal powders. It covers documentation and traceability, sampling, particle-size distribution, chemistry, loose and tapped density, morphology, flowability, contamination checks, and packaging/storage rules. Want to laser-diffract particle sizes or run a Hall flowmeter? The procedures are baked into 52907, letting shops validate powder lots and benchmark different suppliers. It even sets tests for recycled powder so you can prove that used material is still up to snuff.
Polymer powders follow similar characterizations — size, moisture, melt-flow index — though a polymer-specific ISO twin has yet to match 52907’s depth. Current practice blends generic plastics tests (ISO 1133 for melt flow, for example) with SLS vendor specs, but a dedicated international standard is on the horizon.
Beyond plastics and metals, AM also taps photopolymer resins (for SLA) and ceramic or composite powders. Viscosity curves, cure kinetics, and shelf life rely on general chemistry tests for now; process-tailored standards are still maturing.
Finally, ASTM issues alloy-specific specs that AM parts must hit. ASTM F2924 locks down chemistry and mechanical minima for AM-grade Ti-6Al-4V, while ASTM F3055 does the same for Inconel 625 printed via PBF. Such specs guarantee that an AM-built bracket can stand shoulder-to-shoulder with its forged counterpart — a non-negotiable in aerospace and defense.
Design Standards
Additive manufacturing (AM, often simply called 3D printing) achieves reliable results only when sound materials and sound design techniques work hand-in-hand. Unlike conventional methods, AM offers virtually unlimited geometric freedom—but that freedom comes with fresh ground rules. Designers must weigh up the need for support structures, layer-driven mechanical anisotropy, surface roughness, and tight tolerances right from the CAD stage.
ISO/ASTM 52910:2018 is the broad-spectrum playbook for AM design. It sketches what to consider—no matter which AM process you use—so engineers can squeeze every drop of potential from the technology. The standard defines “AM-friendly part characteristics” and flags “AM-specific constraints.” It also dives into strategies that only AM enables, such as topology optimisation, lattice structures, and internal flow channels. Think of 52910 as both a design checklist and a roadmap for companies folding AM into product development.
Because every AM process has its quirks, ISO/ASTM backed 52910 with deeper, process-specific design rules. Powder bed fusion (PBF) needs especially sharp guidance, and the ISO/ASTM 52911 series fills that gap:
ISO/ASTM 52911-1:2019 zeroes in on laser-based metal PBF (PBF-LB/M). It answers nuts-and-bolts questions such as minimum wall thickness, optimum overhang angles for support, and how to lay out channels or holes. It also tackles thermal distortion and stress—baked-in hurdles of metal PBF—and distils proven best practices into one up-to-date guide. Veteran designers treat 52911-1 as a reference; newcomers, as a textbook.
ISO/ASTM 52911-2:2019 delivers similar wisdom for laser-based polymer PBF (PBF-LB/P)—the classic SLS playground. Polymer PBF rarely needs supports, so the focus shifts to part orientation, multi-part nesting, and how powder reuse affects a build. It explains how to offset polymer shrinkage during cooling and how clever design nudges up surface quality. In essence, the standard bottles years of SLS shop-floor know-how for the next wave of designers.
Design standards pay off in the real world. A well-designed, standards-compliant part may print with fewer supports, suffer fewer failures, and need less post-processing. GE Aviation’s fuel nozzle proves the point: once machined from 20 pieces, it now prints as a single part thanks to principles championed in 52910. Topology optimisation lightened the nozzle, internal channels and supports were dialled in, and the finished component sailed through aviation certification—lighter, stronger, and cheaper to make.
Production Process and Equipment Standards
Design and material choices are only half the story; the production process itself must be nailed down. Calibration, parameter control, machine consistency, and safety all decide whether a print run succeeds repeatably. To that end, a cluster of standards spells out how to qualify both hardware and workflow.
In metal PBF, reliability is king. ISO/ASTM 52904:2019 (adopted from ASTM F3303-18) lays out how to prove that a laser- or electron-beam machine can build critical parts. It details machine calibration, parameter optimisation, repeatability checks, and sensor verification. For instance, you test whether laser power is uniform across the bed and whether parts from different build plates hit the same mechanical marks. Operators must re-qualify machines at set intervals—vital when the parts in question might hold aircraft or human lives in the balance.
To benchmark a printer, many shops build a standard test artefact. ISO/ASTM 52902:2019 defines one packed with columns, holes, thin walls, and angled ramps. You print it, measure it against CAD, and crunch numbers for dimensional accuracy and surface finish. Buyers use it to accept new machines; technicians print it after maintenance to prove the rig is still in spec.
(Illustration: NIST’s reference artefact for gauging an AM system’s knack for complex geometry. Regularly printing and measuring such a part tracks machine stability over time.)
Process and equipment rules reach beyond metal. ISO/ASTM 52903-2:2020 states baseline gear requirements for material-extrusion printers—heater accuracy, bed-levelling tolerance, filament feed stability, and so on. Broader machine-safety norms (ISO 12100 risk assessments, laser-safety codes) likewise apply, plus AM-specific matters like inert-gas enclosures, powder filtration, and emergency-stop provisions. Manufacturers must document compliance to earn CE marks and similar certifications.
In practice, these production standards act as an AM machine’s quality passport. Print the 52902 artefact on schedule and you’ll catch drift before it ruins parts. Qualify your workflow under 52904 and you gain hard evidence of process capability—reassuring customers and auditors alike. Standards are what haul AM from one-off prototypes to full-blown industrial production.
Post-Processing Standards
Additively-manufactured parts aren’t always ready for prime time the moment you pop them off the build plate. Post-processing steps—heat treatments, support removal, surface finishing, powder clean-out—often stand between a “green” print and a flight-ready component. For metal AM you might stress-relieve, HIP the part, shot-blast it, then machine critical faces; plastics get their own spa day with support-dissolving baths, sanding, maybe a splash of paint. Standardising these chores is essential for rock-steady quality, yet post-processing in AM is still very much a moving target.
The first big push has come from ASTM. Take ASTM F3301-18 “Additive Manufacturing—Post-Processing Methods—Guide.” It walks shops through safe support removal, micro-structure-friendly heat treatment, polishing routes, and dimensional finishing—say, a quick spin on the CNC for that sealing surface. Same story in the works for space hardware: draft ASTM WK65929 zeroes in on laser-PBF spacecraft parts and how to finish them without nasty surprises. The goal is simple—turn a raw AM build into a predictable, certifiable end product.
No ISO-branded rulebook exists yet for post-processing, so the community borrows from general standards and proven shop wisdom. Furnace controls? AMS 2750. Grit-blasting? The relevant ISO surface-finish spec. Saw-cutting and de-powdering? Lean on generic safety and machining codes. Until ISO/ASTM writes dedicated documents, printers stitch together their own procedures, audit them hard, and keep quality on a tight leash.
Documentation is the other half of the equation. If a titanium part goes through HIP, every second of temperature-pressure-time has to be logged and verified. Expect ISO/ASTM to publish focused standards for these bread-and-butter steps down the road; until then, firms craft in-house specs and police them under broader quality-management umbrellas—which, spoiler alert, we unpack in the next section.
Test and Quality-Control Standards
Quality assurance in AM lives and dies by rigorous testing plus bullet-proof record-keeping. We’re talking mechanical and physical tests to prove the part hits its marks and audits to prove the process was buttoned-up from powder lot to shipping crate. A whole constellation of standards keeps that galaxy in orbit.
Start with the workhorse ISO/ASTM 52901. Beyond freezing requirements into a purchase order, 52901 forces buyer and supplier to agree—up front—on every inspection step: how many fatigue coupons, which tensile spec, what metrology tools, and the pass/fail gates (say, ≥ X MPa tensile strength, ± Y mm dimensional tolerance). In short, QC becomes a contractual obligation, not an after-thought.
Mechanical tests ride on mainstream material standards: ISO 6892-1 or ASTM E8/E8M for metals; ISO 527 for plastics. AM’s twist is build orientation—an X-direction tensile bar can out-muscle its Z-direction twin, so reports must shout the print direction. Enter ASTM F2971-13, which standardises everything from machine make and layer thickness to any post-build treatment, ensuring labs compare apples to apples, not apples to space shuttles.
Dimensional and visual inspections follow suit. Terminology from ISO 52921 pins down coordinate systems in metrology reports. Gear like CMMs and 3-D scanners obey their usual calibration laws, but AM’s labyrinthine geometries often demand CT scanning. ASTM E1441 guides industrial CT, and new papers drill into porosity hunting or flaw mapping inside printed parts.
Material integrity is a chapter all its own. Microscopy, porosity counts, radiography—standards steer each check. Allowed pore fractions might trace back to a material spec; X-ray acceptance levels could mirror ASTM E1921. Aviation regulators, meanwhile, treat AM like casting until dedicated criteria mature: “Same pores, same rules.”
Finally, the umbrella systems. Any shop, from scrappy start-up to aerospace giant, is expected to run an ISO 9001-grade quality-management system. AM, though, layers on extra traceability. DIN SPEC 17071:2019 spells out what an AM plant must track—org charts, staff skills, machine quals, in-process monitoring, powder lots, you name it. Each build gets its own “traveller” file logging machine ID, material batch, operator, parameters, calibrations, part locations. Should a widget misbehave in service, trace-back is a phone call, not a manhunt. DIN’s playbook is already under CEN review and may evolve into ISO/ASTM 52920, giving the world a unified yardstick. In the end, quality control isn’t just testing the part; it’s safeguarding the whole value chain—and that only works when the standards interlock like gears.
Standards Specific to Different 3-D Printing Technologies and Sample Industrial Cases
Additive manufacturing isn’t a single trick pony; it’s an umbrella for a whole toolbox of 3D printing processes, each driven by its own physics, materials, and sweet-spot applications. In the next pages we’ll zoom in on four of the most common platforms — Material Extrusion (FDM), Polymer Powder Bed Fusion (SLS), Vat Photopolymerisation (SLA/DLP), and Metal Powder Bed Fusion (DMLS/SLM) — and map out the key standards plus real-world use cases for each.
Material Extrusion (FDM)
Fused Deposition Modeling works by melting a slender thermoplastic filament and laying it down in tidy noodles, layer after layer. These days you’ll spot FDM everywhere, from weekend-maker machines on a bedroom desk to hulking industrial units cranking out engineering prototypes.
Quality in FDM lives or dies on three pillars: the filament itself, rock-solid machine calibration, and sensible slicer settings. ISO/ASTM 52903-1 / -2 spell out material and hardware requirements. Imagine a small-to-medium shop running a farm of FDM printers; they insist every roll of PLA comes with a 52903-1 certificate guaranteeing tight diameter tolerance. They also run a pre-print checklist — nozzle clean ✔, bed leveled ✔ — to squeeze out variability before it bites.
Because FDM parts wear that tell-tale “layer staircase,” design matters. ISO/ASTM 52910 steps in here: orient parts to slash support usage, tip wide overhangs into shallow self-supporting slopes, and you’ll save print time and post-cleaning grief.
Real-world snapshot: a machinery OEM bangs out functional prototypes on FDM rigs. Every time they swap filament spools, they oven-dry and weigh samples to confirm moisture is below spec — ASTM D4442 is their playbook. If a print hiccups later, they can prove “Moisture was in range, so the fault lies elsewhere.” Even a compact outfit can run a tight, standards-driven ship.
Polymer Powder Bed Fusion (SLS)
Selective Laser Sintering spreads a hair-thin coat of polymer powder — most often PA 12 — and zaps it with a laser. Because the unsintered powder props up the part, you print complex, support-free geometries sturdy enough for real-use loads: think auto prototypes, custom orthotics, even snazzy eyewear frames.
Here, powder quality and thermal discipline rule the roost. While ISO/ASTM 52907 focuses on metal powders, the same logic applies: track particle-size distribution, shape, moisture, and oxidation. A service bureau running EOS machines checks each PA 12 lot against supplier certs; if flow-rate or median size drifts off-spec, the shipment goes straight back.
Design-wise, ISO/ASTM 52911-2 gives SLS-specific tips. Because you can pack many parts in one build, proper nesting matters: leave breathing room so heat doesn’t pool and warp the batch. The standard’s rules on spacing and layer-time balance are baked into most professional slicers.
Picture a med-tech firm printing custom ankle braces. They follow 52910 plus 52911-2: smooth radii instead of knife-sharp corners, wall-thickness tuned to tame residual stress. Before printing they run a moisture test on the powder; after printing they let the cake cool slowly to dodge distortion. Less trial-and-error, more first-time-right.
Vat Photopolymerisation (SLA/DLP)
Stereolithography cures a vat of photosensitive resin layer by ultra-thin layer. The payoff? Silky surfaces and micron-level detail, perfect for dental models, jewellery masters, and bioprint research.
Standards here lean on machine calibration and material safety. Resins arrive with full SDS sheets; storage temp, shelf life, and viscosity are checked per ASTM D445 or equivalent.
Designers still live under the umbrella of 52910, but SLA has one quirk: it needs supports. Many vendors advise anything flatter than 45° gets propped up. Good practice is to nudge contact points to hidden faces so the sanding later is painless.
Fresh SLA parts usually pass through an IPA wash and a UV curing oven. Safety and quality here tap generic standards like IEC 60825 (laser/UV safety).
Take dentistry: a clear-aligner lab prints trays with a Class IIa certified resin that sailed through ISO 10993 biocompatibility trials. Because the supplier anchors claims in that standard, the clinic can prove patient safety without juggling extra tests.
Metal Powder Bed Fusion (DMLS/SLM)
Laser-based metal PBF (DMLS, SLM, pick your acronym) fuses fine metal powder into near-wrought-density parts. Pair that with wild design freedom and you get game-changing components in aerospace, medical implants, and energy.
Because failure here is pricey—or downright dangerous—ISO/ASTM 52904 is the gospel of process qualification. Before a fuel-nozzle or turbine blade ever takes flight, the machine’s laser map, atmosphere control, and scan strategy all pass the 52904 checklist. Repeatability isn’t a hope, it’s documented fact.
On the design front, ISO/ASTM 52911-1 dives into support-strategy, self-supporting angles, and distortion hacks. Need a big flat plate? The standard suggests baking in a slight pre-bow or a lattice cut-out pattern so thermal stress can relax gracefully.
Material properties hinge on post-heat-treat recipes, so QA involves tensile, hardness, and fatigue tests. A Ti-6Al-4V build might be judged against ASTM F2924 minimums; porosity limits borrow from casting codes until AM-specific ones land.
Real-world proof? Jet-engine giants like Rolls-Royce demand suppliers print 30-plus coupons, document every parameter per ASTM F2971, and match strength & fatigue targets before green-lighting production. The same rigor shows up in custom implants: manufacturers fold the whole line into an ISO 13485 QMS and validate each step with 52904-style evidence. Bottom line—no standard compliance, no sale.
Metal AM is where the standards orchestra plays at full volume; from powder spec to final CT scan, each note is written in a different clause—but the symphony keeps planes flying and patients healing.
Industrial Approaches, Real-World Applications, and Why Sticking to Standards Matters
To truly appreciate the practical value of additive-manufacturing (AM) standards, it pays to look at how companies of every size—from aerospace giants to scrappy start-ups—fold those standards into their daily routines.
Big-league manufacturers tend to keep a phone-book-thick checklist of references when they weave AM into serial production. Picture a jet-engine builder: its in-house paperwork cites dozens of norms, starting with the ISO/ASTM 529XX series and running through aerospace-specific specs such as the SAE AMS materials suite and regulatory must-haves from FAA/EASA. Even when the company writes its own “Titanium Powder Acceptance” spec, it still leans on ISO/ASTM 52907 for test methods—just with tighter tolerances. Complying isn’t merely about quality; it’s about liability and market access. Skip a standard and, in a worst-case scenario, the firm could face grounding orders or courtroom drama.
For small and mid-sized businesses (SMEs), standards can be a secret weapon rather than red tape. Take an auto-parts supplier that wants to stand out by 3D-printing functional metal parts. Cash might be tight, but earning an ISO 9001 badge—while wiring AM processes into that quality system—tells potential clients, “Our shop is under control.” In fact, a buyer’s RFQ may flat-out demand an ISO/ASTM 52901-driven technical agreement. Nail that requirement and the order is yours; miss it and a competitor swoops in.
Space agencies such as NASA are just as keen on the rulebook. When NASA hot-fired a copper rocket-chamber and nozzle made via AM back in 2020, the team relied on established or in-house-adapted standards at every turn—from powder purity checks to post-build heat cycles and brutal test protocols. The upshot? The additively built hardware shrugged off the same hellish temperatures and pressures that legacy parts endure.
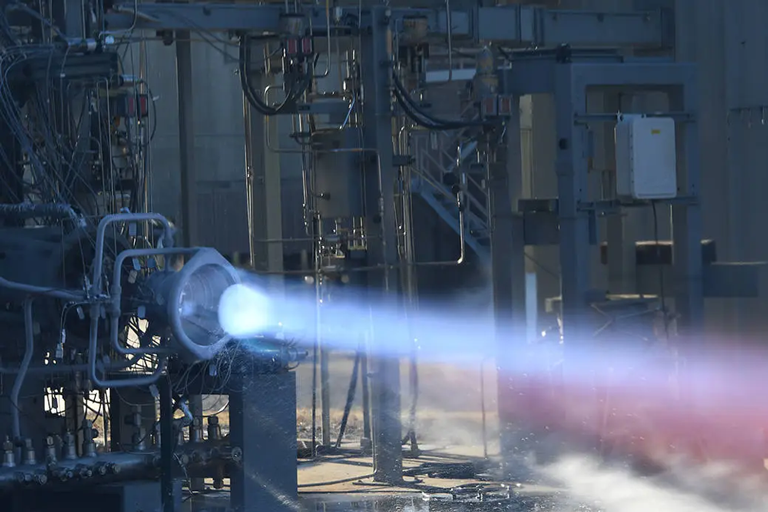
Figure: Hot-fire test of NASA’s additively manufactured copper combustion chamber and nozzle (November 2020). The success story rests on rock-solid choices in design, material selection, and quality control—all benchmarked against recognized standards.
Shared 3d printing and additive manufacturing standards don’t just police industry; they turbo-charge innovation. With a common yardstick, labs and companies can swap data without playing translation bingo. Imagine a university group studying a brand-new alloy: if they log their results in line with ASTM F2971, another lab can compare notes instantly. The same dynamic fuels cross-company road-maps and sector-wide consortia.
In short, treating standards as allies—not chores—unlocks quality, safety, and efficiency in AM. The ISO/ASTM 52900 family stitches together a seamless quality chain, and new chapters will keep emerging as the tech matures—think in-situ monitoring or sustainability metrics for recycled powder and energy use. Whether you’re a blue-chip aerospace titan or a garage-level entrepreneur, success in AM hinges on one mindset: “Think standard first.” Follow the playbook and you’ll turn bold ideas into trustworthy products, helping additive manufacturing earn its rightful place in mainstream industry.
References
NASA. (2020, November 17). 3D-printed rocket parts: The future of spacecraft. NASA. Retrieved from https://www.nasa.gov/image-article/3d-printed-rocket-parts-future-of-spacecraft
CEN. (2020). prEN ISO/ASTM 52903-1: Additive manufacturing — Material extrusion-based additive manufacturing of plastic materials — Part 1: Feedstock materials. iTeh Standards Store. Retrieved from https://standards.iteh.ai/catalog/standards/cen/0d108029-5db1-4aa6-a00b-0a9f5020c14f/pren-iso-astm-52903-1
Schwab, S., & Marquardt, M. (2020). Analysis of general and specific standardization developments in additive manufacturing from a materials and technological approach. ResearchGate. Retrieved from https://www.researchgate.net/publication/342458531
NIST. (n.d.). Additive manufacturing test artifacts and benchmarks. National Institute of Standards and Technology (NIST). Retrieved from https://www.nist.gov/el/intelligent-systems-division-73500/production-systems-group/nist-additive-manufacturing-test
Springer. (2023). Benchmarking the performance of additive manufacturing systems for industrial applications. Journal of Materials Engineering and Performance. Retrieved from https://link.springer.com/article/10.1007/s11665-023-07897-3
Ventola, C. L. (2014). Medical applications for 3D printing: Current and projected uses. Pharmacy and Therapeutics, 39(10), 704–711. Retrieved from https://pmc.ncbi.nlm.nih.gov/articles/PMC4487294/
DIN. (2017). DIN EN ISO/ASTM 52921: Additive manufacturing — Coordinate systems and test methodologies. ANSI Webstore. Retrieved from https://webstore.ansi.org/standards/din/dinenisoastm529212017
NASA. (2019). Characterization of copper alloy fabricated by laser powder bed fusion additive manufacturing for propulsion applications. NASA Technical Reports Server (NTRS). Retrieved from https://ntrs.nasa.gov/api/citations/20190002140/downloads/20190002140.pdf
NIST. (n.d.). Manufacturing standards and measurement science for additive manufacturing. National Institute of Standards and Technology (NIST). Retrieved from https://www.nist.gov/manufacturing