What Is Vat Photopolymerization? A Guide to Resin-Based 3D Printing
3D printing technology, with its time-saving structure in manufacturing processes and resource-optimizing nature, has reshaped production methods in countless industries. This additive manufacturing approach covers everything from prototyping all the way to final product fabrication. Among the most widely utilized 3D printing methods is Vat Photopolymerization (VP), favored by hobbyists, professionals, and manufacturers who want prints with micron-level detail and a sleek finish. While VP shares some common ground with another widespread technique, FDM 3D Printing, it truly shines when projects demand extremely fine details. In particular, VP printers excel at producing complex geometries, thin-walled designs, and models that call for top-notch surface quality.
Vat Photopolymerization and Its Varieties
Vat Photopolymerization technology fundamentally works by hardening liquid photopolymer resins with UV light at specific wavelengths. This resin is poured into a transparent-bottomed vat—hence the name “Vat” Photopolymerization.
During printing, a metal build platform submerges into the resin. Once it nears that transparent, liquid interface, the very first layer solidifies upon exposure to the UV light. You can think of the resin’s curing as the point where the light prompts molecular bonds to form—monomer chains linking up into polymers—ultimately hardening the layer in place.
After each layer sets, the platform lifts by a few microns along the Z-axis, and new layers form in the same manner. Print resolution relates directly to the tiniest detail a printer can achieve; it’s defined by the precision of X, Y, and Z movements plus the beam or light source diameter. In VP technology, resolution can be stated in micrometers (µm) or DPI (dots per inch). Of all the settings we can tweak, layer height (Z resolution) is the single most important. The thinner the layer, the sharper the detail and smoother the surface—though that inevitably increases total print time.
Vat Photopolymerization encompasses Stereolithography (SLA), Digital Light Processing (DLP), and Liquid Crystal Display (LCD/mSLA) methods, all popular with makers, hobbyists, engineers, and designers. In the medical field—especially dentistry and orthodontics—such techniques produce highly precise models and devices. Since dental prostheses require both complexity and extreme accuracy, 3D SLA technology is especially pivotal here. By leveraging SLA, near-flawless implant planning and personalized dental prosthetics can be manufactured with almost no margin for error.
Aside from these three main techniques, there are also advanced VP methods like Two-Photon Polymerization (2PP) and Continuous Liquid Interface Production (CLIP). Still, for our purposes, we’re focusing on the three principal Vat Photopolymerization processes most prevalent in clinical and commercial spheres.
SLA 3D PRINTING
3D SLA printing relies on a powerful laser to cure each layer of photopolymer resin. This setup can handle multiple objects on a larger build platform without compromising quality. SLA-printed pieces often exhibit incredibly detailed surfaces. With layer heights spanning roughly 25 to 100 microns (0.025–0.1 mm), it’s possible to achieve especially high-resolution prints. Meanwhile, X and Y resolution (dots per inch) depends on the laser spot size and servo motor accuracy, generally ranging from about 30 to 140 microns (0.03–0.14 mm).
A concentrated laser beam scans each layer point by point inside the resin tank, solidifying the material layer by layer until the model emerges in full.
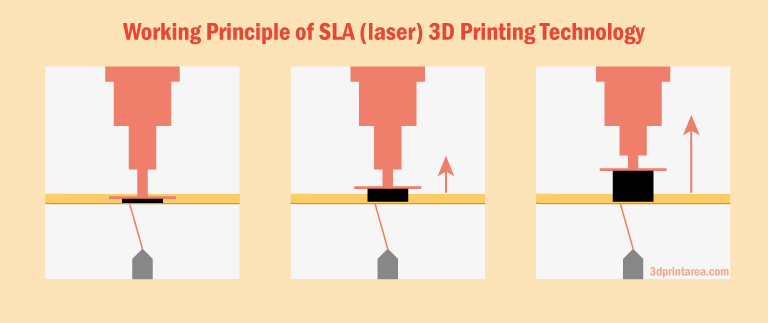
DLP 3D Printing
3D DLP printing is similar to SLA but substitutes a Digital Micromirror Device (DMD) for the laser. It uses UV light to harden photopolymer resin, though the mechanism differs slightly. One big advantage is that each layer can cure in one go, drastically speeding up production times. In plain terms, no matter how large a given layer’s surface area is, that layer still cures in the same amount of time.
Light from the projector solidifies each layer in a single flash, cutting print durations compared to point-by-point scanning.
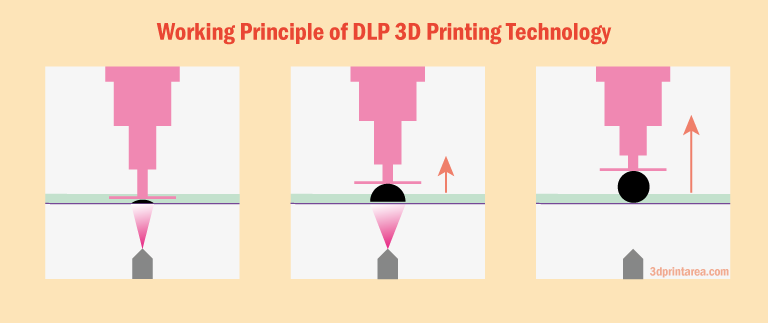
DLP is a top choice in dental clinics, especially for quick, single-visit (chairside) procedures. Indeed, this is the only 3D printing technology that enables real-time restorations during one appointment, a game-changer for modern dentistry.
LCD/mSLA 3D Printing
3D LCD printing shares many traits with DLP—so much so that it’s often grouped in the same category. Still, it does have distinct features. An LED projector is stationed behind the LCD panel under the resin tank. The LCD filters ultraviolet light so that it only shines where the resin needs to harden. Because these LCD displays frequently offer resolutions above 4K, LCD/mSLA printers can deliver remarkably fine print quality.
LED light is filtered through an LCD screen, curing only the regions belonging to that specific layer all at once.
Lately, LCD 3D printers have become more affordable thanks to variations with lower production costs and less optimization overhead. These machines are targeted at non-medical fields, which means it’s now totally feasible to snag an LCD 3D printer for a fraction of what you’d pay for most SLA or DLP models.
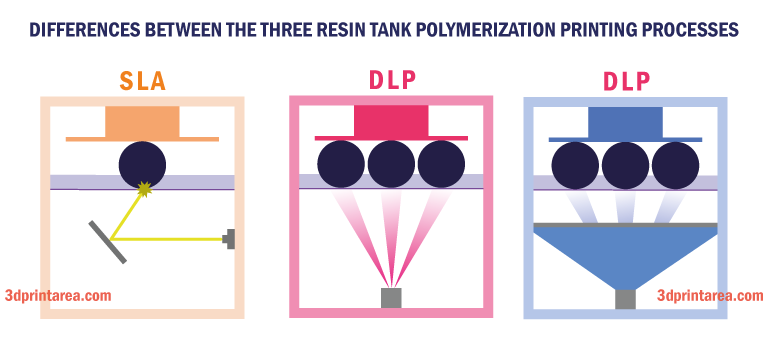
Technologies in Comparison
Print Time
When it comes to print time, DLP and LCD hold a distinct advantage over SLA, mostly because SLA relies on a laser tracing each layer, while the other two technologies cure the entire layer in one go. Of course, the kind of resin you use—its physical and chemical characteristics—plus your build platform and print volume also factor into how long the overall process will take.
Another critical point is the use of robots that can automatically jumpstart new prints after one finishes. Some companies encourage these robotic setups to boost production speed. Once the print is done, a robot can pick up the finished part and start a new job without any human intervention. Clever, right?
Accuracy
SLA 3D printing shines because it maintains consistent accuracy regardless of build volume. DLP, on the other hand, can show variations in precision tied to the print size, though software improvements have largely helped counterbalance that drawback. LCD printers sometimes struggle with optical convergence issues, but there hasn’t been sufficient scientific research to definitively assess how this affects print accuracy. Based on available studies, though, smaller DLP prints can outperform SLA in resolution and accuracy.
Ease of Use
This factor typically isn’t tied strictly to the underlying technology, but among budget-friendly printers, LCD 3D printers have a reputation for being more ergonomic. Factors that influence ease of use include whether the printer utilizes open-source software, how automated the post-print finishing steps are, the specific resin tank technology involved, and—like we mentioned earlier—robotic and AI-driven supports that can simplify the workflow.
Scientific Test on Object Placement in the Build Platform
A study by Caussin and colleagues at Paris Cité University compared results based on how objects were arranged on the build platform. Angling or orienting each object in certain ways directly impacted print duration, accuracy, and the likelihood of errors.
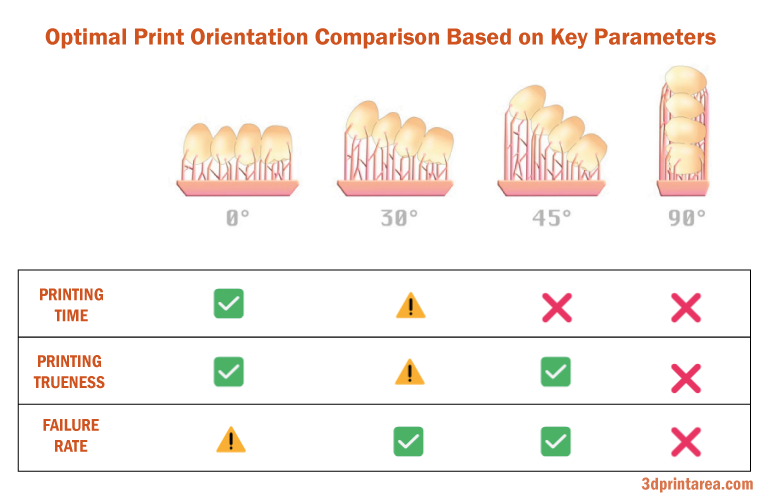
Post-Processing
Modeling and Slicing: Models created with CAD software are sliced into layers the printer can interpret, producing the necessary code files. At this stage—just like the test we mentioned earlier—careful placement of objects on the build platform can significantly affect the printing workflow.
Printing Phase: Whether you’re using SLA, DLP, or LCD, each layer is cured into shape, ultimately building the object layer by layer.
Post-Processing (Cleaning and Curing):
Resin Cleaning: After the print finishes, the object is rinsed with isopropyl alcohol or other solvents.
Additional UV Curing: Exposing the part to extra UV light boosts its biocompatibility and mechanical strength.
Final Touches (Polishing, Painting, Coating)
Removing Support Structures: Supports that formed during printing need to be carefully taken off so the interior surfaces aren’t damaged.
Biocompatibility Standards
Regardless of which 3D printing method is used, any dental prosthesis or appliance must meet ISO 10993-1 and FDA standards for biocompatibility. Scientific tests have shown that some photopolymers aren’t suitable for extended intraoral use. Experimental work on improving resin biocompatibility focuses on fine-tuning the polymerization process, aiming for a safer production cycle.
What Does the Future Hold for Vat Photopolymerization 3D Printing Technology?
Like most fields, 3D printing technology is on track to grow in tandem with artificial intelligence. Plenty of research is already underway, particularly in bioprinting. Thanks to these advancements, vat photopolymerization (VP) 3D printing—commonly used in medical settings—may soon print hard dental tissues and, with AI-driven systems, even customized soft tissues at the same time. Innovations in biocompatible materials, AI support, and growing industry know-how suggest that both 3D printing and VP technology will continue to thrive.
References
Caussin, E., Moussally, C., Le Goff, S., Fasham, T., Troizier-Cheyne, M., Tapie, L., Dursun, E., Attal, J.-P., & François, P. (2024). Vat photopolymerization 3D printing in dentistry: A comprehensive review of actual popular technologies. Materials, 17(4), 950.
Vat Photopolymerization powers SLA, DLP, and LCD resin 3D printing technologies, and is recognized as a core additive manufacturing category by Loughborough University.