3D and 4D Printing Multistable Structures: The Future of Adaptive Materials
What is 3d Printing?
Three-dimensional (3D) printing is an evolving and increasingly widespread technology that enables the production of complex structures and personalized manufacturing. This technology has advanced significantly in recent years, leading to innovations like 4D printing multistable structures, which add time-responsive capabilities to printed objects. By using appropriate 3D printing techniques based on the intended application, high-resolution parts can be produced. This printing process is carried out by adding material layer by layer, which is why this technology is also known as additive manufacturing. The development of 4D printing multistable structures represents the next frontier in this field, allowing printed objects to change shape in response to environmental stimuli. Since 3D printing provides cost-effective solutions for customization and prototyping, it is frequently preferred in the manufacturing industry, with 4D printing expanding these capabilities even further.
Let’s briefly discuss some commonly used 3D printing technologies
Types of 3d Printing
- Stereolithography (SLA): This method utilizes photopolymerization to cure light-sensitive liquids layer by layer, forming a 3D structure.
- Digital Light Processing (DLP): Similar to SLA, but instead of a laser, it uses a projector as a light source, allowing for faster printing.
- Direct Laser Writing (DLW): Uses ultra-fast laser pulses to create objects with high precision.
- Selective Laser Sintering (SLS): This technique selectively sinters metal and ceramic powders to build objects.
- Fused Deposition Modeling (FDM): A 3D printing technology that employs the material extrusion technique. In this method, thermoplastic materials are melted and extruded through a nozzle to form objects. Being the most cost-effective and widely used technique, FDM is preferred by both amateurs and professionals.
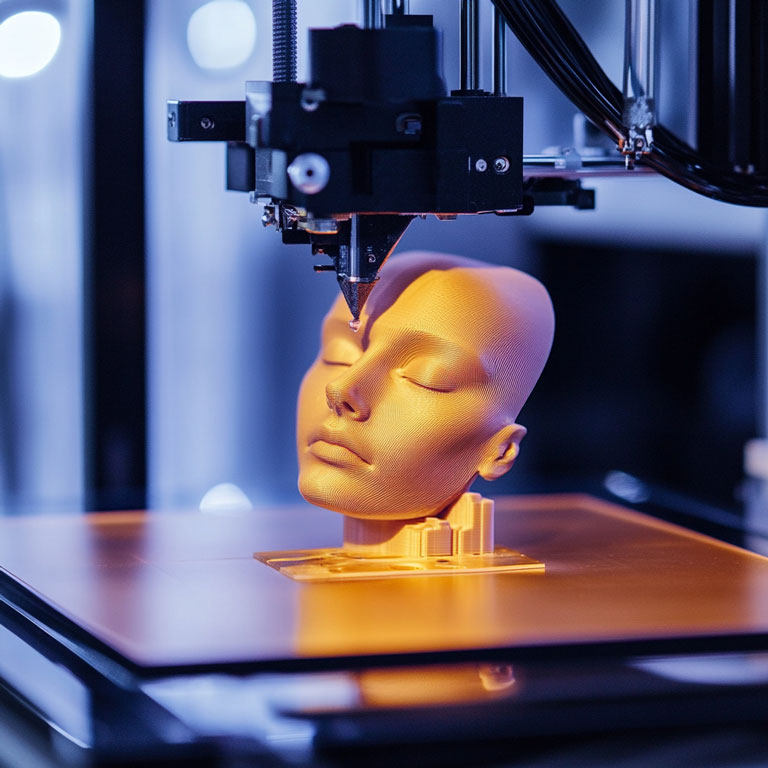
What is 4D Printing?
Today, 3D printing applications have diversified and integrated with new technologies. One of these emerging technologies is 4D printing.
4D printing extends 3D printing by introducing a fourth dimension: time, allowing 3D-printed structures to exhibit dynamic, responsive functions over time. This technology is typically achieved by printing smart materials that can respond to environmental stimuli. Some of these materials include liquid crystal elastomers (LCEs), hydrogels, and shape memory polymers (SMPs).
4D-printed structures are sometimes referred to as programmable matter. Essentially, 4D printing technology enables 3D-printed structures to change shape in response to variables such as heat, water, light, and pH levels.
Let’s examine the study “3D and 4D Printing of Multistable Structures” published in the journal Applied Sciences, which explores the potential of 3D and 4D printing in engineering applications.
In the examples presented in the study:
- Figure (1) shows a 4D-printed object made of liquid crystal elastomers (LCEs) responding to different temperatures. The structure undergoes a pre-programmed shape transformation.
- Figure (2) demonstrates a 4D-printed object made of hydrogels, which bends when submerged in water.
- Figure (3) illustrates a 4D-printed structure designed to react to different colors of light, deforming in distinct ways depending on the light color.
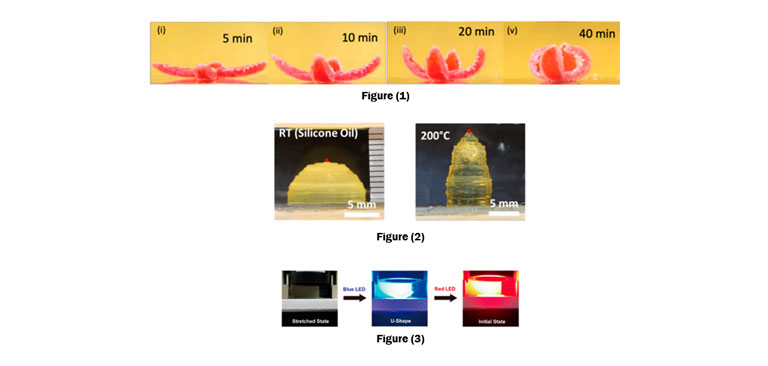
Multistable Structures
Multistability refers to a system or mechanical structure possessing multiple stable states. But what does a stable state mean? A stable state is a condition where a system, after experiencing an external force or disturbance, can return to one of its predefined positions.
In multistable systems, each structure is designed to have multiple stable configurations, meaning it can adopt different shapes while maintaining mechanical stability. These systems can transition between different stable forms, similar to a clicking mechanism, where the structure shifts between configurations and remains in an energy-efficient state.
One of the key advantages of multistability is that a single structure can perform multiple functions. This ability can be described as offering shape adaptability or multiple operational modes depending on external stimuli.
For example, one method to facilitate transition between different configurations is to apply pre-stress to the layers of a material or structure. This technique can be used to program a structure’s deformation behavior, allowing it to switch between stable states under specific conditions.
3D Printing of Mechanical Multistable Structures
Strained Layer
One of the ideal ways to achieve mechanical multistability is by utilizing pre-strained layers. In 3D printing, residual thermal stress, which is typically considered an undesired effect that distorts printed structures, can actually be turned into an advantage to create multistable structures.
In the image below, a 3D-printed hemispherical structure made of liquid crystal elastomers (LCEs) is shown. Due to the molecular alignment of the material, the structure expands at 200°C.
Compliant Mechanism
Compliant mechanisms are another method to achieve mechanical multistability using 3D printing technology. When 3D-printed structures contain sufficiently thin beams, these structures can exhibit bistable or multistable behavior through bending and flexing.
4D Printing Multistable Structures: Mechanical Applications and Innovations
Heat-Responsive Structures
4D printing involves the use of smart materials, such as shape memory polymers (SMPs). SMPs are known as smart materials that can “remember” a permanent shape. When these materials are heated above a specific transition temperature, they soften and become reshapable. At this stage, a temporary shape can be set. Once cooled, SMPs regain significant rigidity, a process referred to as thermomechanical programming.
In the image below, a robot swimming in warm water is shown. The robot’s structure incorporates a bistable mechanism and shape memory polymer (SMP) strips. These strips are normally held in a stretched state, but when the transition temperature is exceeded, the shape memory effect is activated, and the strips return to their original shape. By repeating this cycle through temperature changes, the robot can swim autonomously in water.
Solvent-Responsive Structures
Multistable structures produced through 3D printing and designed to be responsive to external stimuli have been utilized in advanced applications, such as logic operations. These applications take advantage of the different behaviors exhibited by structures with multiple stable states when exposed to different solvents or stimuli.
Glass Fiber (GF) Reinforced PDMS
First, a PDMS (polydimethylsiloxane) composite reinforced with glass fiber (GF) was used to selectively absorb non-polar solvents such as toluene. When these structures are immersed in a toluene bath, they can rapidly switch between a monostable or bistable state. Due to their fast response time, these structures are considered a promising option for high-speed applications, such as logic gates.
Hydrogel + Nanofibrillated Cellulose (NFC)
Similar to GF-reinforced PDMS, a hydrogel composite containing nanofibrillated cellulose (NFC) is used to create bistable structures that respond to water. NFC restricts the isotropic expansion of the hydrogel in water, allowing it to swell perpendicular to the printing direction in a controlled manner. As a result, these structures can also exhibit either bistable or monostable behavior.
By applying solvents such as water and toluene, selectively activated bistable structures have been used to create logic gates, including AND, OR, and NAND, which are fundamental components of digital logic systems.