3D Printing in Aerospace and Defense: Powering the Next Flight Frontier
3D Printing in Aerospace and Defense is propelling two innovation-driven sectors toward unprecedented speed and precision. The aerospace and defense industries, which require innovation and precision, are evolving rapidly. One of the leading technologies driving this rapid advancement is 3D printing, also known as additive manufacturing, which offers solutions tailored to these innovation and precision needs.
In this article, we will explore how 3D printing impacts these high-risk industries and examine its applications.
How Does the Aerospace Industry Benefit from 3D Printing? The Role of 3D Printing in Aerospace and Defense
Revolutionary Advances in Design Freedom
Traditional manufacturing methods often pose challenges in complex design processes due to mold usage and machining limitations. 3D printing removes these barriers, enabling the creation of intricate and unique designs. This capability significantly enhances productivity in critical areas for companies.
Let’s take a closer look at the next-generation antenna developed by Lockheed Martin, a leading American company operating in the Aerospace, Defense, and Security sectors, which was produced using 3D printing for space deployment.
This antenna is Lockheed Martin’s first complex hardware produced using 3D printing. According to the company, while it shares similarities with previous versions, instead of being manually soldered piece by piece, the new version was manufactured as a single component using 3D printing.
As seen, major companies are now utilizing new technologies such as 3D printing instead of traditional design and manufacturing methods.
This process is easily repeatable, eliminating variability in manufacturing and testing processes. By adopting this technology, we can produce components with tighter tolerances compared to handmade parts.
Larry Loh, Director of Advanced Manufacturing at Lockheed Martin.
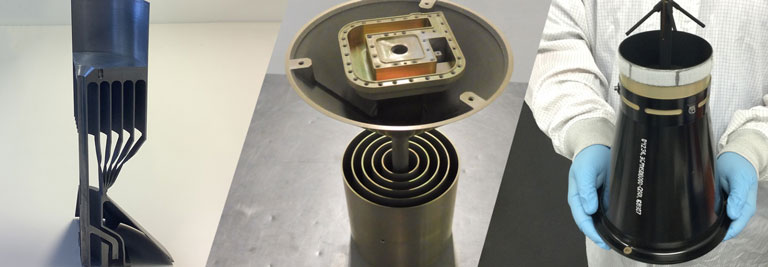
Shortened Delivery Times and On-Demand Production
Time plays a critical role in the aerospace and defense industry. In addition to managing complex technological processes, companies must also minimize delivery times due to factors such as competition, security, and urgent demand. One of the key advantages of 3D printing technology is its ability to facilitate on-site production, allowing for on-demand manufacturing when needed.
Let’s explore the innovative applications of the U.S. military, which, as part of the Convergence 21 initiative, enables soldiers to quickly manufacture essential components during combat situations using RFAB (Rapid Fabrication via Additive Manufacturing on the Battlefield) and 3D printing technology.
The Convergence 21 project aims to enhance and support the military’s operational capabilities on the battlefield by equipping soldiers with the right systems. Clearly, one of the most crucial technologies in this system is 3D printing, which provides the military with on-demand production capabilities.
Additionally, at the U.S. military’s facility in South Korea, RFAB enables 3D printers to manufacture essential components such as tank parts, truck components, rifle parts, and many other critical supplies required by the army.
Increased Efficiency with Lightweight Components
One of the biggest advantages of 3D printing is its ability to produce lightweight yet durable components that can withstand high loads. Just like in the automotive industry, every gram saved in the aerospace and defense sectors contributes to significant fuel savings, leading to a substantial reduction in emissions.
Fuel efficiency and low emissions not only enhance the operational capabilities of manufactured systems but also play an active role in ensuring the sustainability of defense infrastructures.
A notable example of how 3D printing reduces product weight and creates significant advantages can be seen in Boeing’s 787 Dreamliner model. In this model, large-scale 3D printers were used to manufacture fuel nozzles, resulting in a 25% weight reduction.
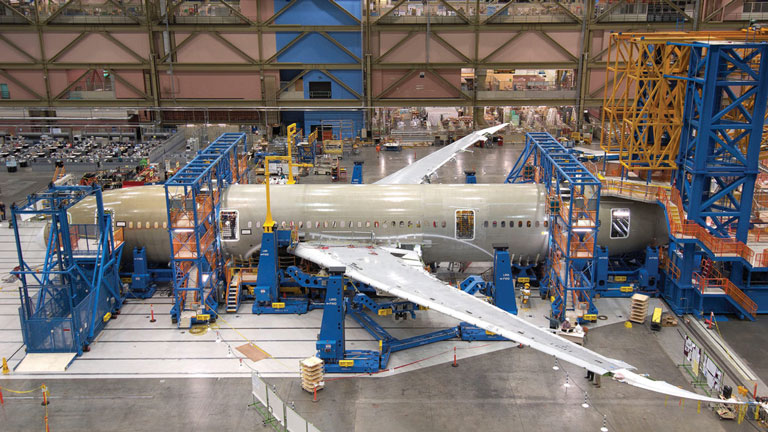
Cost Efficiency and Material Optimization
In the aerospace and defense industries, high-performance yet difficult-to-machine and costly materials such as titanium are commonly used. With additive manufacturing, only the required amount of material is utilized, significantly reducing material waste and optimizing resource usage.
Founded in 2007, Norsk Titanium is a company specializing in aerospace manufacturing, producing critical aircraft components for models like the Boeing 787.
Due to titanium’s growing importance in aerospace, Norsk Titanium prefers this material. Additionally, since traditional machining methods (such as CNC milling) generate large amounts of excess material, Norsk has adopted additive manufacturing (3D printing) to achieve material savings and cost efficiency.
In the aerospace and defense sector, where precision and efficiency are paramount, Norsk has pioneered its proprietary Rapid Plasma Deposition (RPD) technique—a 3D printing innovation that replaces traditional Powder Bed Fusion. By utilizing titanium wire instead of powder, RPD enables faster, more cost-effective production of high-performance components, advancing additive manufacturing capabilities for critical aerospace and defense applications.
With this 3D printing technology, Norsk can manufacture a 2 kg titanium part using only 6 kg of titanium wire, compared to traditional methods that require cutting from a 30 kg titanium block—a major advancement in material efficiency.
References
Aerospace America. “Making 3D-printed Parts for Boeing 787s.”
Lockheed Martin. “3D-Printed GPS Antenna: A Pathfinder for Future Satellites.”
DVIDS. “Project Convergence 21 – RFAB 3D Printing (Image 3 of 3).”
“3D Printing in Aerospace and Defense: A Review of Technological Breakthroughs and Applications.”