Additive Manufacturing or Subtractive Manufacturing? Why Not Hybrid?
Additive and subtractive manufacturing methods are two fundamental production techniques that form the backbone of modern industries. Evolving industrial needs and innovative solutions have brought these methods to their current advanced states. The core principles of Additive vs Subtractive Manufacturing are distinct: Additive manufacturing, commonly known as 3D printing, allows for the creation of complex and custom designs by adding material layer by layer, while the traditional subtractive manufacturing method enables the production of precise components by removing material. But is it possible to combine the advantages of both methods? Yes, hybrid manufacturing is an innovative production method that brings together the best of both worlds.
In this guide, we will explore additive manufacturing, subtractive manufacturing, and hybrid systems that integrate the two approaches in detail. Supported by academic studies, we will delve into the differences, advantages, disadvantages, and innovative applications of these methods.
What is Additive Manufacturing?
Additive manufacturing, widely known as 3D printing, is a production technology that can directly create objects from computer models tailored to specific needs. Unlike subtractive manufacturing methods, additive manufacturing allows for more practical and rapid production of customized structures.
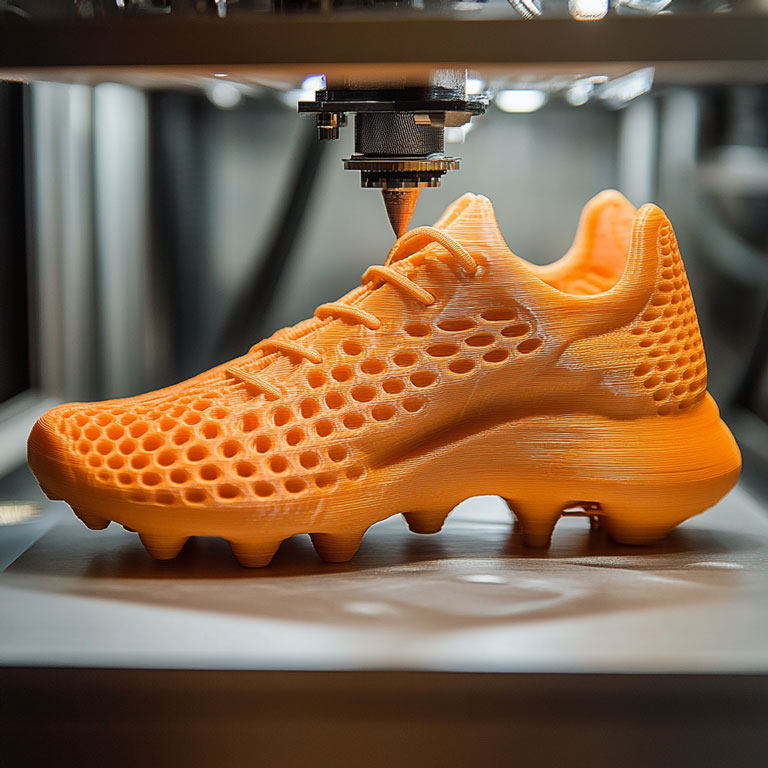
Advancements in 3D printing technologies are progressing so rapidly that the technologies described here might already be outdated by the time you read this. Let’s take a quick look at the most common 3D printing technologies!
1- Material Extrusion
This technology produces objects by melting thermoplastics through a nozzle and depositing them layer by layer. The most commonly used materials include plastics such as PLA, ABS, PETG, TPU, and nylon. The most well-known method in this category is FDM.
- FDM (Fused Deposition Modeling
- Fused Filament Fabrication (FFF)
2- Vat Polymerization
This type of additive manufacturing is based on solidifying liquid photopolymer materials in a tank using light, layer by layer. Various resins are used in these processes. The most well-known techniques are SLA and DLP.
- Stereolithography (SLA)
- Digital Light Processing (DLP)
3- Powder Bed Fusion
This 3D printing technology works by selectively melting or sintering a thin layer of powder to create layered structures. The range of materials is extensive, including metals like stainless steel, titanium, and aluminum, as well as various polymers and ceramics. Techniques include SLS, SLM, DMLS, and EBM.
- Selective Laser Sintering (SLS)
- Selective Laser Melting (SLM)
- Direct Metal Laser Sintering (DMLS)
- Electron Beam Melting (EBM)
4- Binder Jetting
This method operates by selectively spraying a binder liquid onto a thin layer of powder spread over the build area. Materials used include stainless steel, bronze, titanium, aluminum, ceramics, sand, and various polymers.
5- Sheet Lamination
This 3D printing technique enables the production of parts by bonding thin sheets layer by layer using heat, pressure, or adhesive. Materials such as metals, paper, plastics, and composites are used.
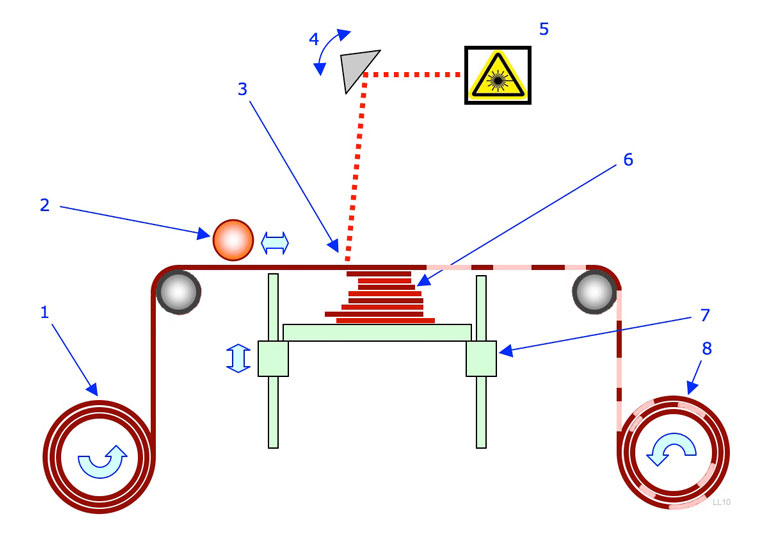
6- Direct Energy Deposition
This technology relies on melting metal powders or wires using an energy source and depositing them layer by layer. It uses materials such as various metals, composites, and, less commonly, ceramics (mainly in applications requiring high strength).
Advantages of Additive Manufacturing
- Suitable for producing customized and complex parts.
- Prevents the use of unnecessary materials during production.
- Reduces logistics costs by enabling on-site manufacturing.
- Eliminates the need for molds and special tools, reducing equipment requirements.
Limitations of Additive Manufacturing
- Surface quality
- Production volume limitations
- Potential weaknesses in mechanical strength due to the layered structure
- Material limitations
What is Subtractive Manufacturing?
Subtractive manufacturing encompasses most traditional manufacturing methods, where an object is created by cutting, drilling, turning, milling, grinding, reaming, or carving material from an initial solid block, plate, or rod of raw material. In this process, excess material is removed until the final product is achieved. While these processes can sometimes be done manually, they are most commonly performed using computer-assisted methods.
The most widely used computer-assisted technology is Computer Numerical Control (CNC). Other subtractive manufacturing methods include laser cutting, water jet cutting, electrical discharge machining (EDM), and plasma cutting.
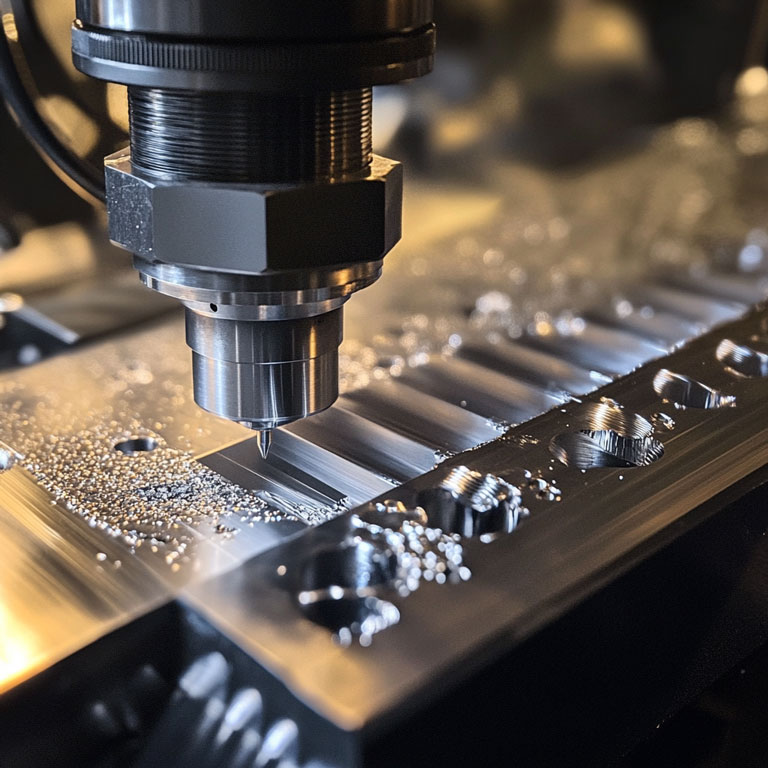
CNC Machining Process:
Designing the model in a digital environment
The process begins with designing the model using Computer-Aided Design (CAD) to define the product’s geometry and design details.Creating G-code instructions
Using the CAD model, Computer-Aided Manufacturing (CAM) software generates G-code instructions, which are operational commands for CNC machines.Producing the final product
CNC machines execute these commands to perform mechanical operations such as turning, drilling, boring, milling, and reaming. These operations transform the raw material block into a finished and ready-to-use product.
Other Subtractive Manufacturing Processes
Laser Cutting
Water Jet Cutting
This method uses high-pressure water combined with an abrasive substance to cut materials. Being a cold process, it offers advantages like preventing thermal deformation. Common materials include stone, ceramics, glass, plastic, composites, and metals.
Electrical Discharge Machining (EDM)
This method removes material by generating sparks between an electrode and the workpiece. It is ideal for complex designs requiring high precision. It can be applied to electrically conductive metals.
Plasma Cutting
Plasma cutting works by ionizing gas with electricity to create plasma, which can quickly and efficiently cut metals. It is especially suitable for cutting thick metals cleanly and precisely. Common materials include steel and aluminum.
Advantages of Subtractive Manufacturing
- Extremely smooth surfaces can be achieved.
- Durable products can be obtained due to the homogeneous material structure.
- Ideal for mass production.
- Offers a wide variety of materials.
- Established production techniques with well-defined standards.
Limitations of Subtractive Manufacturing
- A large amount of material waste can be generated during the production process.
- Not suitable for very complex products due to manufacturing techniques.
- The tools used in the manufacturing process wear out over time, leading to additional costs.
- High initial costs.
- High energy consumption.
A Comparison: Additive vs Subtractive Manufacturing (AM and SM)
Criteria | Additive Manufacturing (AM) | Subtractive Manufacturing (SM) |
---|---|---|
Complexity | Highly complex and detailed geometries can be easily produced. | Limited capabilities for designs that require high complexity and detail. |
Accuracy | Tolerance levels typically range between 0.1mm and 0.2mm, depending on the technology used. | Offers very high precision, with tolerances as low as 0.01mm. |
Initial Setup | Simple to set up in almost any environment, particularly the production space. After assembling the 3D printer following the instructions, calibration is performed, and production can begin with a CAD design converted to G-code. | More complex and time-consuming to set up and start production. Certain environmental requirements must be met, as not all spaces are suitable for subtractive manufacturing. Calibration processes are more intricate due to the higher precision required. The complexity of the devices also varies depending on the technologies used. |
Cost | Material costs per kilogram are generally higher, but material waste is minimized. Additive manufacturing uses only the necessary amount of material. | While the cost per kilogram of raw material is lower, up to 70% of the material may be wasted during production. |
Speed | Faster for producing complex structures. It is also advantageous for small parts and prototyping processes compared to SM. | More advantageous in terms of speed for producing large and simple geometries. |
Mass Production | Not suitable for mass production. The need to print each part individually makes it less efficient for large-scale manufacturing. | Techniques like injection molding and other mold-based methods are suitable for mass production. Other SM techniques can also be optimized for production lines. |
Surface Quality | Products made with this technology are typically not ready for direct use and may require post-processing. Processes like surface smoothing, sanding, painting, or coating are often necessary to improve the finish. | Produces highly precise surfaces and detailed features, often with minimal need for post-processing. It is well-suited for processes requiring smooth finishes and high detail. |
Choosing Between Additive Manufacturing and Subtractive Manufacturing
When choosing between Additive Manufacturing (AM) and Subtractive Manufacturing (SM), it is essential to evaluate specific criteria based on the requirements of the project. As outlined in the comparison table, factors such as complexity, accuracy, initial setup, cost, speed, and suitability for mass production play a critical role in determining which manufacturing method is more appropriate.
In today’s rapidly evolving world, where these technologies continue to advance at a fast pace, it is equally important to stay updated with the latest innovations alongside these well-established considerations.
Why Not Hybrid?
The hybrid manufacturing model combines additive manufacturing (AM) and subtractive manufacturing (SM) to maximize efficiency in production processes. This model leverages the strengths of both technologies, enabling the production of precise and durable parts. Hybrid manufacturing combines the ability of additive manufacturing to produce complex and customized geometries with the advantages of subtractive manufacturing, such as achieving smooth surfaces, to create advanced products.
Let’s dive deeper into the subject by examining a scientific study on hybrid manufacturing.
In this scientific study, High-Nitrogen Steel (HNS) containing 0.7% nitrogen, known for its high strength and toughness, was used. The high nitrogen content in this material poses certain challenges during additive manufacturing (AM) and can negatively affect the mechanical properties of the final product. Issues such as nitrogen loss and leakage during production can impact the mechanical properties of the material.
Let’s take a closer look at the findings of this study!
In these experiments, the microstructures and tensile properties of two High-Nitrogen Steel (HNS) samples, produced using Wire-feed Additive Manufacturing (WAAM) and Hybrid Additive/Subtractive Manufacturing (HASM) methods, were systematically compared. The HASM system used in the production combines a Wire Arc Additive Manufacturing system with a five-axis CNC milling subtraction system, enabling highly precise hybrid manufacturing.
The two samples prepared for the experiment are shown below:
(a) represents the sample prepared using WAAM.
(b) represents the sample prepared using HASM.
It is clearly observed that the side surface smoothness is significantly higher in the sample produced using the hybrid system (b) compared to the one produced using WAAM (a).
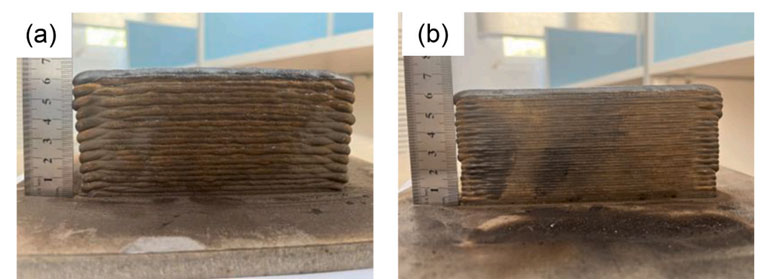
Another test involved analyzing the side surface smoothness of the samples using a 3D scanner. (a) represents WAAM, while (b) represents HASM. According to the point cloud data of the selected region, WAAM falls within the yellow region, which represents higher values. In contrast, HASM is located in the green region, corresponding to lower values. This scanning result confirms that HASM has a smoother side surface.
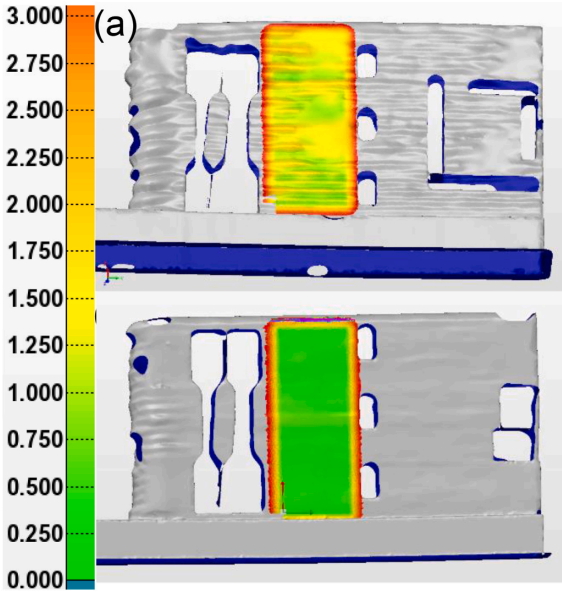
Another test conducted was the porosity test, which aimed to compare the number of pores in the samples. It is worth mentioning again that surface pores are undesirable features. 😊
Using small strips extracted from both samples, an Industrial Computed Tomography (CT) scan was performed. Image (a) shows the strip sample taken from the WAAM-produced part, while image (b) represents the strip sample taken from the HASM-produced part.
Pores were present in both samples; however, the number of pores in the HASM sample was significantly lower compared to the WAAM sample. According to the provided data, the defect volume ratio in the WAAM sample was as high as 73%, whereas in the HASM sample, this ratio was only 19%. This indicates a significant reduction in defect volume.
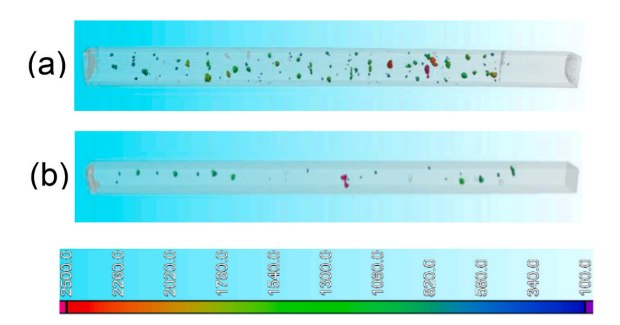
When examining the pore diameter and density distribution, it was determined that the maximum pore diameter in the WAAM sample was 2.439 mm, while in the HASM sample, the maximum pore diameter was 1.303 mm. This represents an almost 50% reduction in maximum pore size.
As previously observed in the test results, the pore density in the WAAM sample is significantly higher compared to the HASM sample.
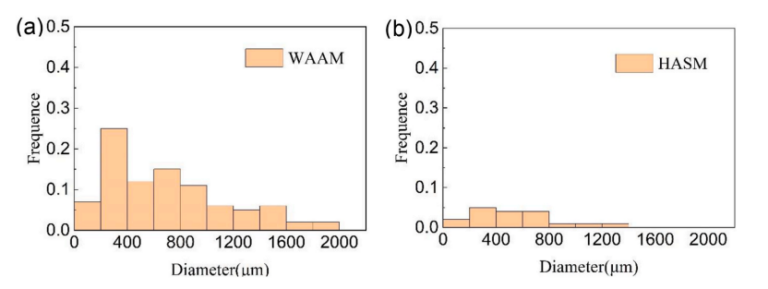
Finally, let’s examine the tensile test performance of the two samples. Three key parameters are considered: Yield Strength (YS), which represents the elastic limit and the maximum stress a material can withstand before plastic deformation; Ultimate Tensile Strength (UTS), which indicates the maximum stress a material can endure before breaking; and Elongation, which expresses as a percentage how much the material’s length increases at the moment of fracture compared to its original length.
As observed, all three values are higher in the HASM sample, demonstrating superior mechanical performance.
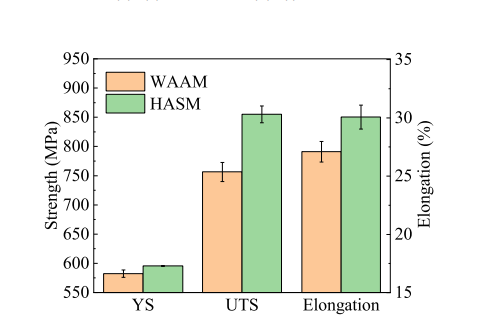
As seen in these experiments, hybrid systems can produce more efficient outcomes by leveraging the advantages of both additive and subtractive manufacturing methods. While each manufacturing technique has certain disadvantages, combining them through hybrid systems helps mitigate these drawbacks to some extent.
The study titled “A Comparison of Wire-feed Additive Manufacturing and Hybrid Additive/Subtractive Manufacturing of High Nitrogen Steel” highlights the potential benefits of hybrid systems in industrial production by utilizing advanced imaging and testing techniques.
References
Qian, M., Song, S., Yang, Z., Guo, Y., & Wang, K. (2024). A comparison of wire-feed additive manufacturing and hybrid additive/subtractive manufacturing of high nitrogen steel. Journal of Materials Research and Technology, 33, 4092–4104. https://doi.org/10.1016/j.jmrt.2024.10.090
Wikipedia contributors. Laminated Object Manufacturing. Wikipedia, The Free Encyclopediaring