3D Printing Revolutionizing Quality and Efficiency in Construction
With the advancement of technology, consumers’ expectations towards production sectors are rapidly increasing, and there is a demand for more innovative and personalized solutions. This situation leads to the emergence of new needs and demands in these sectors. One such sector is the construction industry, where innovations like 3D printing in construction are beginning to address these evolving requirements.
It is known that the construction sector has the largest carbon footprint among all other sectors. Research indicates that this rate is around 40%. With the projected global population growth, it is estimated that 100 billion square meters of new construction will be needed due to housing and infrastructure demands. For these reasons, by leveraging the benefits of new technologies to develop new structural systems, it can play a critical role in reducing global CO2 emissions, saving materials, optimizing energy consumption, and increasing quality and efficiency.
One of the most well-known of these innovative technologies is 3D printing technology. In the construction sector, 3D printing can be considered an additive manufacturing method built in layers, known as masonry construction. Modern additive manufacturing technologies have been adopted by architectural firms since the early 2000s. These innovative applications in the sector have not only reduced processes that previously took a long time down to mere hours but have also resulted in outcomes such as reducing project timelines by dozens of times.
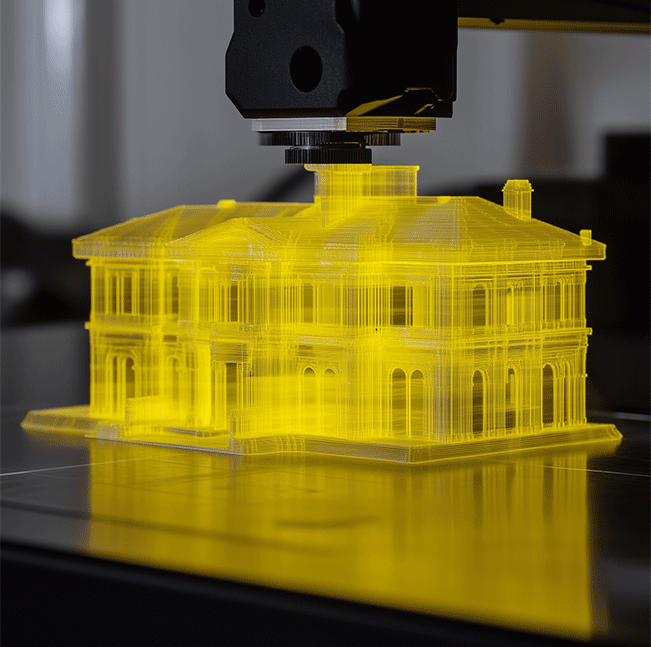
In the study titled “Metal 3D Printing in Construction: A Review of Methods, Research, Applications, Opportunities, and Challenges” published in Engineering Structures magazine, some example projects utilizing 3D technology are discussed. Let us take a look at them together.
Concrete 3D Printing
Concrete is the most widely used raw material globally. It is stated that traditional concrete production techniques involve manufacturing through repetitive molds. Considering that a large portion of concrete construction costs is attributed to scaffolding and formwork, we can anticipate how concrete additive manufacturing techniques can reduce these costs.
It is mentioned that Winsun, a China-based advanced material supplier, conducted research on additive manufacturing and built its first residential building using additive manufacturing technology in 2013. Following this project, in 2016, another building produced through additive manufacturing was manufactured in China and sent to Dubai.
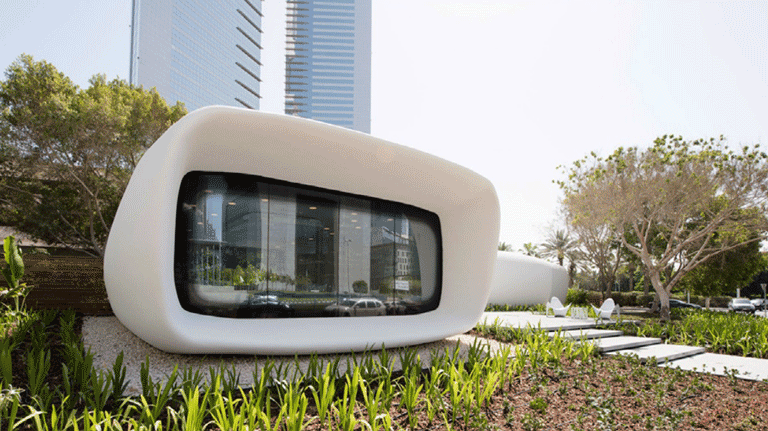
In the study, it is stated that this innovative solution reduces construction costs by 80% and labor costs by 60%.
Additionally, among the structures produced using this technology is the Gemert Concrete Bicycle Bridge, which is reported to be 8 meters long and 3.5 meters wide. This structure, created by casting 1 cm-thick concrete layers, was fabricated in sections and assembled on-site.
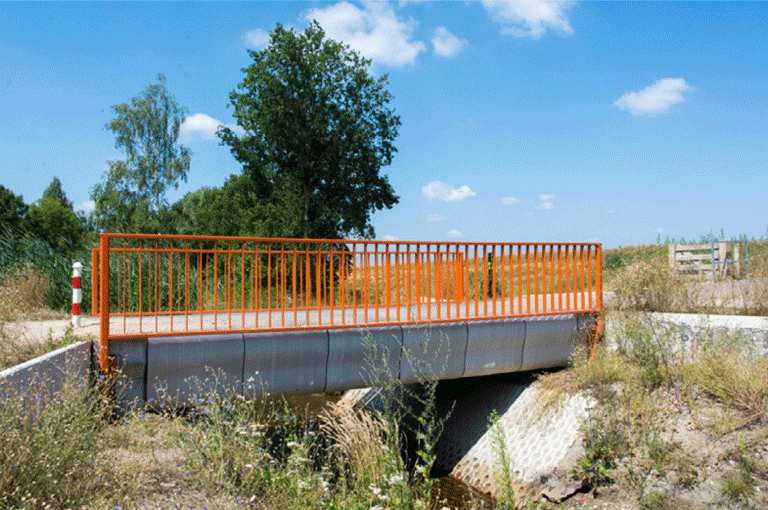
The additive manufacturing method named FreeFAB, developed by Laing O’Rourke, produces the molds used for concrete production using an additive manufacturing process with wax. Molds that traditionally take about 8 days to produce are fabricated within hours using the 3D printing method.
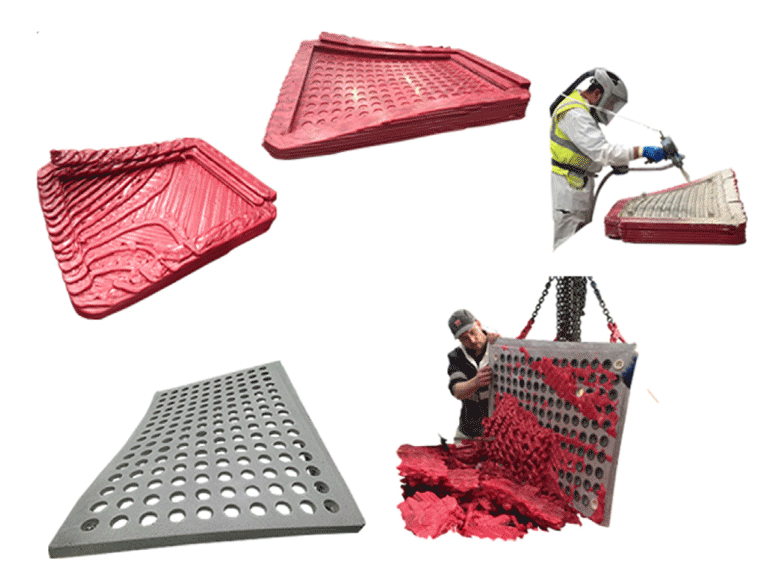
Conclusion: The Impact of 3D Printing in Construction
Technological leaps keep rewriting the rulebook for every sector, and construction is very much in the splash zone. Today’s clients want buildings that are smarter, sleeker, and tuned to their individual tastes. Meanwhile, conventional techniques still stamp a heavy carbon footprint on the planet, even as the global appetite for new infrastructure balloons. 🏗️ Put those pressures together and the case for a rethink becomes impossible to ignore. That’s where “3d printing in construction” steps in—promising leaner workflows, on-demand customization, and a clear path toward greener building practices.
Real-world demos—from Winsun’s printed villas to the nimble FreeFAB process—already showcase how 3d printing in construction can shrink project calendars, slim budgets, and wring every drop of value from raw materials while easing tough manual labor. 🚀 As the hardware scales up and the know-how spreads, this approach is on track to turn the industry upside down, erecting structures faster and cheaper, yet with a sharper eye on ecological impact and resource efficiency.
References
European Commission, Skills for smart industrial specialization and digital transformation, 2019.
Buchanan, C., & Gardner, L. (2019). Metal 3D printing in construction: A review of methods, research, applications, opportunities and challenges. Engineering Structures, 180, 332–348.