3D Printing: What It Is and How It Works
3D printing is an additive manufacturing technology that produces physical parts from computer-aided design (CAD) models using three-dimensional printers. These devices build the desired object by adding material layer by layer. Since the 1980s, 3D printing technology has evolved, granting the manufacturing industry the capability to create architectures that would be very labor-intensive or even impossible to produce with subtractive manufacturing techniques.
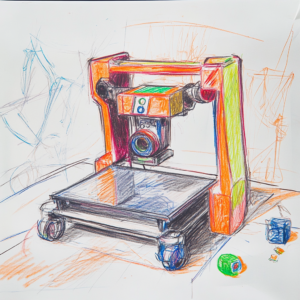
Additive manufacturing provides an opportunity for NASA to produce flight hardware faster and cheaper. We are taking advantage of advanced manufacturing technology that gives us the ability to design and build rocket components that, in some cases, can’t be made any other way.
Chris Singer, Director of the Engineering Directorate at NASA
Standardizing 3D Printing: The Collaborative Role of ISO and ASTM
ASTM and ISO have collaborated to develop the ISO/ASTM 52900 standard in order to establish a common language among professionals interested in additive manufacturing (AM) technology and to facilitate communication. The committees involved in this effort have focused on topics such as test methods, designs, materials, processes, and terminology. Let us begin by discussing some of the terminology associated with this technology.
This technology, widely recognized as additive manufacturing, has been referred to by many different terms during its development. Some of these include additive fabrication (AF), additive processes (APs), additive techniques (ATs), additive layer manufacturing (ALF), layer manufacturing (LM), solid freeform fabrication (SFF), freeform fabrication (FF), rapid prototyping (RP), and rapid manufacturing (RM). In addition to highlighting different aspects of the technology, these terms also serve as indicators of the innovative approaches adopted in manufacturing processes. (Bănică et al., 2024)
While “3D printing” is a more consumer-friendly term, “additive manufacturing” encompasses more industrial and advanced processes.
Traditional methods (for example, the most common one being CNC) operate on the principle of removing material from an initially block-shaped piece through cutting, drilling, and similar processes, whereas 3D printing builds objects by adding layers of material on top of each other. Due to this principle, complex models that are very difficult or even impossible to produce through traditional molding or subtractive manufacturing techniques can be easily manufactured using additive manufacturing. As a mold-free technique, 3D printing stands out as a technology that reduces high costs and production times, and promotes innovation thanks to the design flexibility it offers.
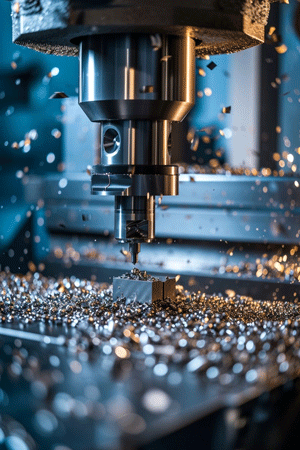
Understanding Different 3D Printing Types and Technologies
1- Material Extrusion
This technology is based on the principle of constructing the design model layer by layer by melting and extruding the material—whether in granular or filament form—through a hot end. Thanks to features such as low cost and ease of use, it is frequently preferred in rapid prototyping applications and hobby projects. Another notable advantage is the wide variety of polymer materials available.
- FDM (Fused Deposition Modeling): It is a Material Extrusion technology that is most preferred by makers and best resonates with the DIY spirit. It operates on the principle of adding layers of thermoplastics (e.g., PLA, ABS, PETG, TPU) that have been melted by a heated nozzle. The operating temperature varies depending on the type of material used.
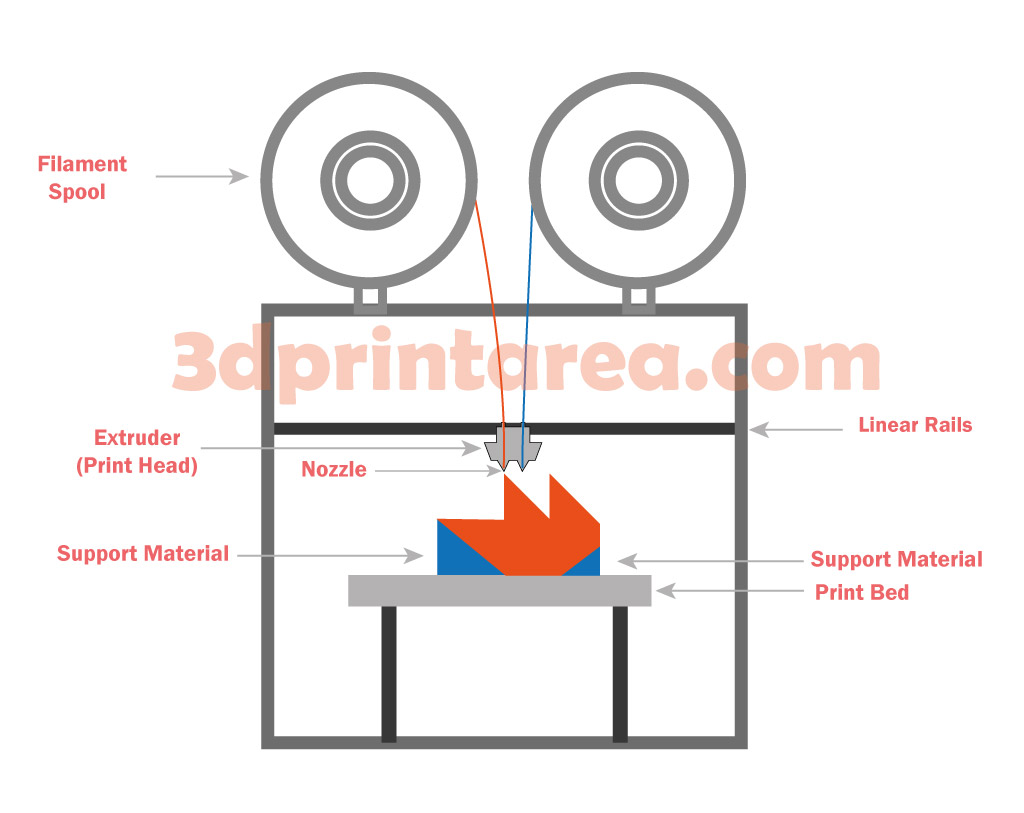
In the article titled “3D-Printing Technology: A Review,” published by the Institute of Electrical and Electronics Engineers at an international conference, which discusses additive manufacturing—particularly the efficiency of the FDM technique and its industrial applications—it is noted that FDM is one of the most widely used printing methods. The study also points out that, despite its many advantages, this technique can only work with polymers; however, there are promising developments involving the metal-specific FDMm technique, which can process metals and thereby expand the range of available materials.
Among the weaknesses of this method, which is suitable for easily producing complex shapes, are the tendency of polymer materials to shrink during the printing process and the lower tensile strength compared to injection molding, due to the layered structure.
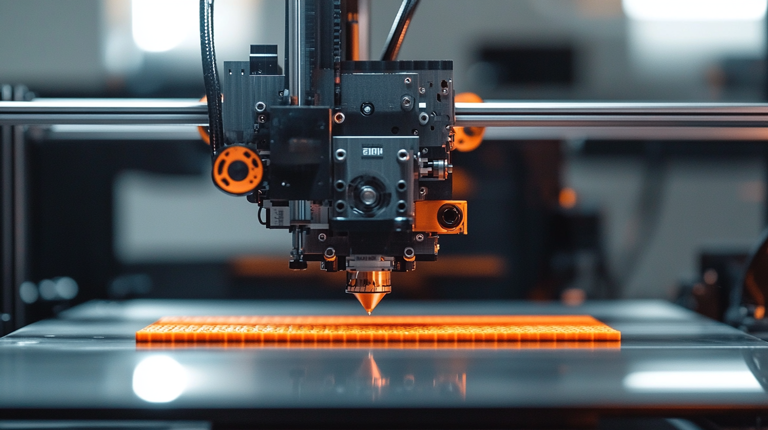
- Fused Filament Fabrication (FFF): Due to the fact that the term “FDM” was trademarked and patented by a company, the open-source community developed the term “FFF.” Its operating principle is the same as that of FDM.
2- Vat Polymerization
- SLA (Stereolithography): Thin layers are formed by curing, i.e., hardening the monomers in the liquid resin with the aid of UV light. These layers constitute the final object. It is one of the Vat Polymerization technologies preferred for applications requiring high precision and detail. Because this technology can produce highly precise products, it is used in industrial design and dental applications. Another advantage is the smooth surface achieved after printing. Owing to this feature, it has become indispensable in certain niche areas.
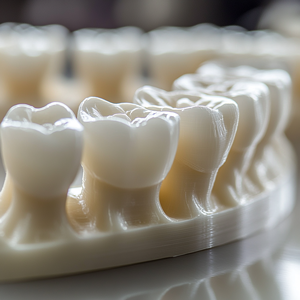
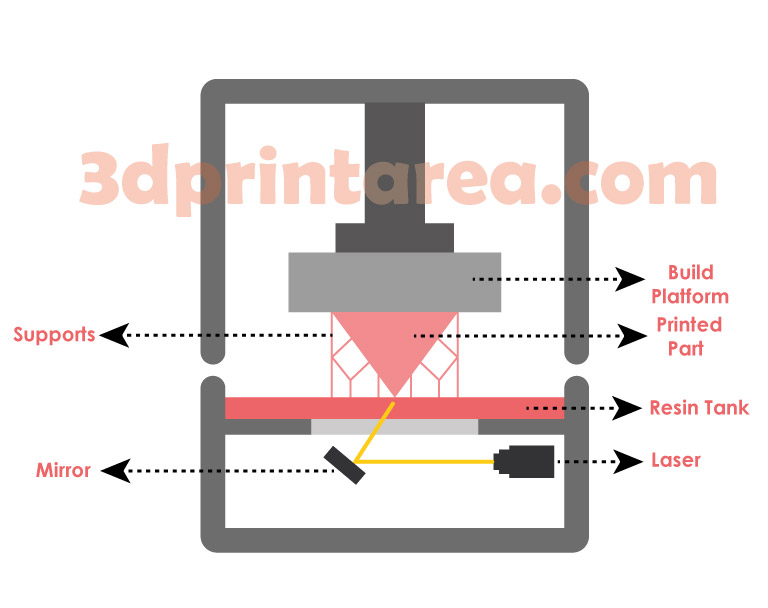
- DLP (Digital Light Processing): This method operates on the same principle as SLA. The only difference is that it uses a digital projector instead of a laser, which allows it to produce much faster than SLA.
3- Binder Jetting
After a thin layer of powder is spread over the powder bed, a liquid with binding properties is sprayed onto specific regions of this bed using a spray head. This process continues until the desired final product is obtained. In this method, a technology similar to Powder Bed Fusion is used.
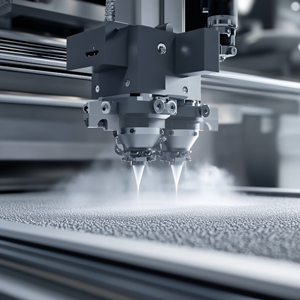
4- Powder Bed Fusion
- SLS (Selective Laser Sintering): In the Powder Bed Fusion technology, a high-powered laser is used. The laser is applied to a thin layer of powder spread over the print bed, selectively sintering (partially melting) the powder to fuse it together. This layer of powder is recreated for each layer. It is widely preferred in industrial production and engineering fields as it enables the production of complex and durable parts.
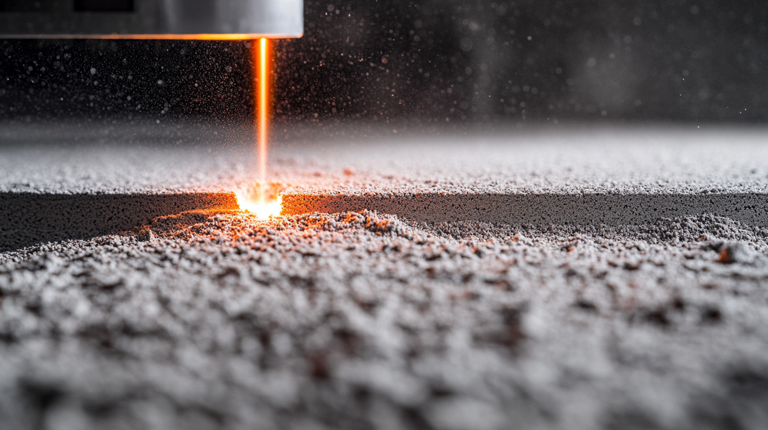
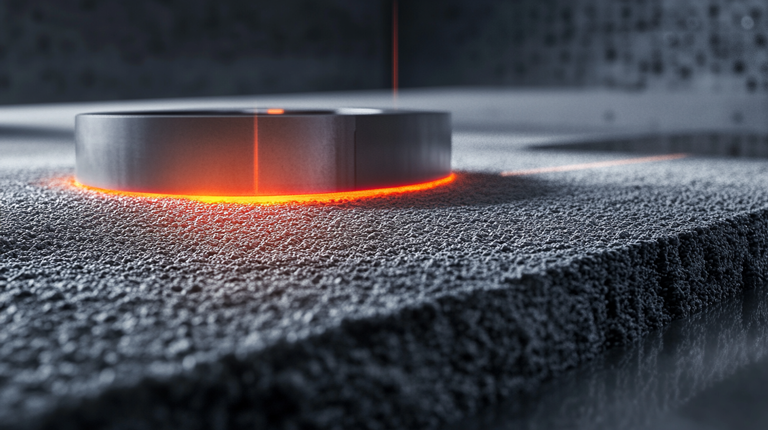
- Direct Metal Laser Sintering (DMLS):
It operates on the principle of selectively partially melting and fusing a thin layer of metal powder using a high-powered laser. This process is repeated layer by layer to produce the desired object.
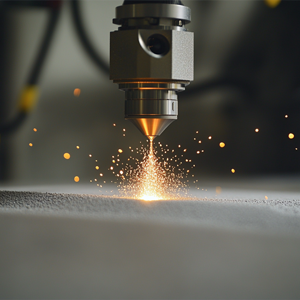
- SLM (Selective Laser Melting): Although similar to the DMLS method, there are technical differences between them. In the SLM method, metals are completely melted to produce denser and stronger parts. In contrast, in DMLS, metal powders are partially melted (sintered).
5- Sheet Lamination
It is a 3D printing technique where the final product is created by adhering or welding thin sheets layer by layer. This technique offers a cost-effective advantage and provides a range of materials such as paper, plastic, and metal. Layers cut into the desired shape are then combined to form the final product. The cutting process can be performed using various methods, including laser, ultrasonic knife, or mechanical cutting.
This technology is suitable for rapid prototyping and aesthetic models. In applications where metal is used as the material, high durability can be achieved. After the product is created, it requires additional post-processing.
6- Direct Energy Deposition
It is a 3D printing technology where metal material in powder or wire form is melted using an energy source to create the desired object layer by layer. In some rare applications, ceramic or polymer powder can also be used. Metal powders are typically derived from metals such as titanium, stainless steel, or aluminum.
This method is ideal for complex shapes but comes with some disadvantages. Products made using this technology are usually rough and may require post-processing. While the wire form prevents material waste, material waste can occur with powder form. It can be said that this is an expensive production technique in terms of cost.
3D PRINTING PROCESS
The 3D objects to be produced are first created using CAD (Computer-Aided Design) software and then converted into STL files. The STL file represents only the external surface geometry of the model and consists of a triangular mesh structure. The next step is slicing the STL file using slicing softwares (PrusaSlicer, Slic3r, Ultimaker Cura, Repetier-Host, SkeinForge, Simplify3d etc).
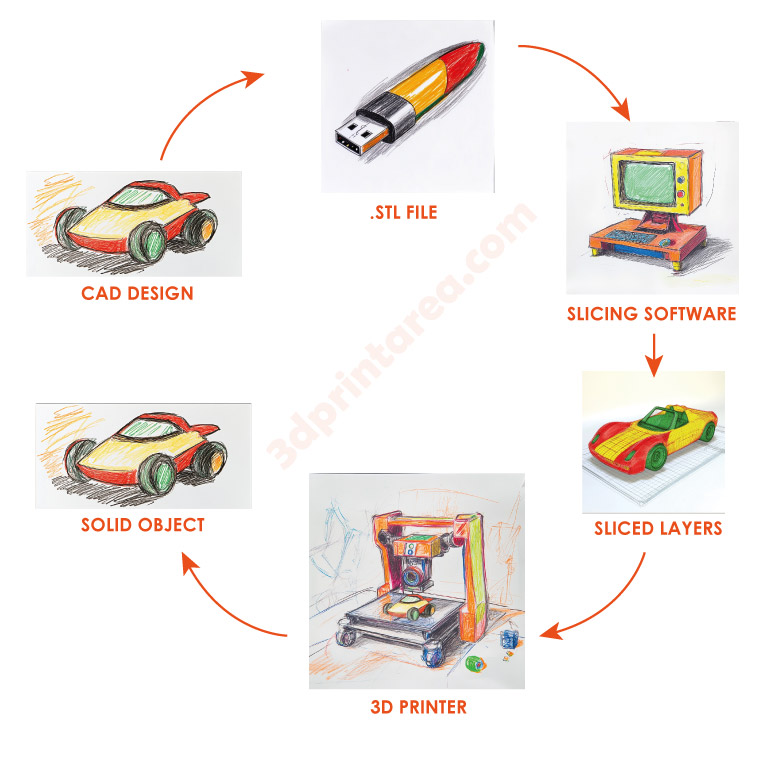
Slicing Process
We can consider the slicing step to be the most critical stage of the 3D printing process. The settings applied at this point directly affect both the success and quality of the print. There are parameters and adjustments at both basic and advanced levels. Let’s take a look at a few of the most fundamental ones together.
Basic steps of slicing:
1- Layer Thickness Adjustment
In this step the layer height is set. The object is sliced into layers which can be thought of as thin cross-sections of the printed object. As shown in the comparison table, when the layer thickness decreases, the print quality and print time generally increase in inverse proportion. The minimum and maximum layer height levels may vary depending on different printers and material types. Below, you can see the sliced view of a 3D printable object. In the zoomed-in image, each detailed layer is 0.28mm thick.
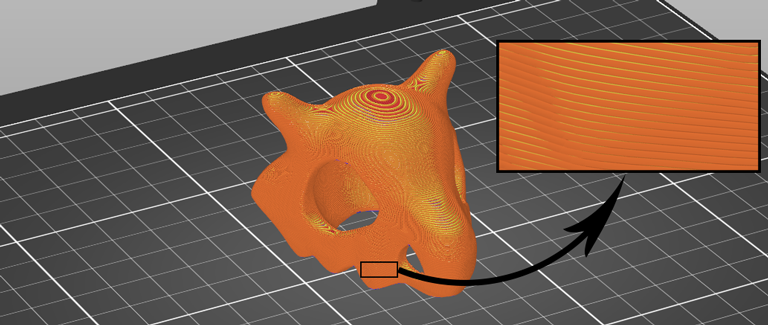
2- Generating Support Structures
In this step, if the object to be printed has overhanging parts, support structures are created by the software. After printing, these support structures are removed from the final object. Support structures are used as auxiliary materials to enable printing of the object’s overhanging sections. The image on the right shows the final desired raven object. The one on the left is the object prepared for printing with support structures. After removing the green support structures post-printing, the raven model will be revealed.
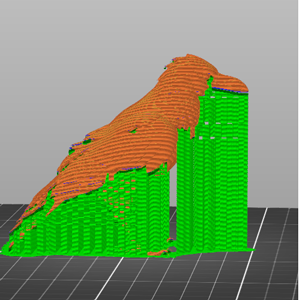
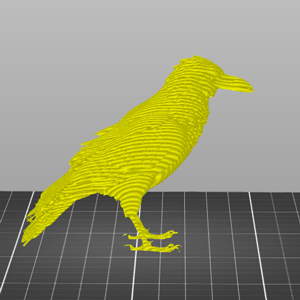
3- Infill Pattern and Density
This is a critical step that affects the strength and durability of the object. In this stage, the pattern and fill density of the object’s internal structure, which is not visible, are determined. The intended use and purpose of the object play a role in deciding these parameters. For example, having 100& infill density for an object used only for decoration may be a waste of material. You can examine the cube object sliced with a 15% infill density and a grid fill pattern.
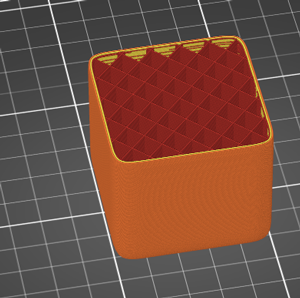
During the slicing process, code files are generated that contains the commands for the printer to understand how to create the object according to our printing preferences. These file formats may vary depending on the printing technology. If we tkaeFDM printers, the most common and well-known type of printing, as an example, the slicing process gives us the G-Code file.
So what is the G Code? G Code consists of commands that contain instructions in a format that 3D printers can understand. It includes commands that control the printer head (extruder) movements, print speed, tempurature settings and other parameters.
Printers using other technologies use file formats that contain commands suited to their own data structures instead of G-Code. These technologies will be explained in detail in the continuation of the topic.
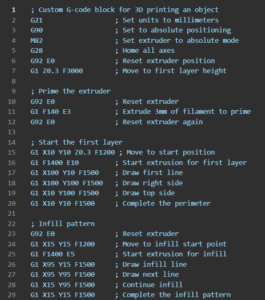
You can explore this topic, where slicing software is compared through scientific testing, and both basic and advanced 3D printing slicing settings are analyzed in detail.
Rapid Prototyping and Rapid Manufacturing
Rapid prototyping, as it is known today, is recognized to have been invented in the 1980s along with 3D printing. Since its invention, this definition has expanded to include various types of production.
3d printing is a low-cost, fast and mold-free technology that enables production in any environment. In short, it allows for the efficient use of time and resources. These factors not only provide direct economic benefits but also play a critical role in reducing manufacturer’s dependency on external sources in production processes. Additionally, complex parts that cannot be produced with traditional manufacturing methods can be easily created with 3D printing.
To briefly list of benefits;
- Cost savings
- Production speed
- Flexibility and customization
- Less material waste
- Environmentally friendly production (Plant-based filaments)
- Reduces storage needs
The Rise and Applications of 3D Printing
Before discussing 3D printing applications, I would like to touch on one of the most appealing aspects of this technology. You’ve probably heard the term “3D printed 3D printer” many times. Imagine a device that, once activated, can produce other devices like itself or easily manufacture spare parts for them or other devices. In a way, it’s limited only by the user’s imagination (and of course, some laws :))
The largest spread in the world of 3D printing occured withthe RepRap Project. This was an open-source Project, allowing anyone tocontribute, and it was a 3D printable 3D printer capable of producing its ownparts. With the RepRap Project, which began in 2004, the process of makinghousehold 3D printers accessible and developable by everyone began.
Let’s watch the RepRap project introduction video together that was released 15 years ago! 🙂
All these developments led to advancements in many areas within the 3D printing World. These Technologies started to be widely used and developed across various industries. As mentioned above, the self-replication ability of 3d printers that can produce their own parts has increased their sustainability, making robotics and prototyping the most extensive application areas.
As mention above, the skill of self renewation of 3d printers that can has ability to produces its parts cause to increas their sustainability, they caused prototyping and robotics became the widest field.
Some fields where 3D printing technology is widely used today include:
- Computers and Robotics
- Medical Applications
- Pharmaceutical Formulations
- Apparel
- Art and Jewellery
- Construction and Home Development
- Education and Research
- Transportation Industries
- Automotive
- Aerospace and Defense
The Future of 3D Printing Technology
Let’s explore how 3D printing (3DP) has evolved and its potential future applications, as outlined in the study titled “Printing the Future Layer by Layer: A Comprehensive Exploration of Additive Manufacturing in the Era of Industry 4.0” published in the journal Applied Sciences.
Additive manufacturing (AM), which has seen significant advancements with Industry 4.0, enables the on-demand production of personalized products by offering innovative opportunities in design and manufacturing. Becoming an integral part of the Fourth Industrial Revolution, AM is adapting to mass production through flexible manufacturing processes.
With the Internet of Things (IoT), 3D printing requires less manual intervention and exhibits enhanced automation capabilities, signaling its evolution toward 4D printing. By adding a fourth dimension—time—4D printing technology enables materials or structures to alter properties such as shape, structure, or function over time under specific conditions. This expands the application areas of 4D printing technology.
Based on materials like shape-memory polymers (SMPs) and liquid crystal elastomers (LCEs), 4D printing is used in fields where adaptive materials are essential and valuable, such as aerospace, regenerative medicine, automotive industries, and soft robotics.
From Industry 4.0 to Industry 5.0: The Next Revolution in Manufacturing
Industry 5.0, born as a response to Industry 4.0, aims to enhance efficiency and quality by integrating robots into automation processes with a human-centered approach, combining them with human creativity. While Industry 4.0 is said to fall short of meeting Europe’s 2030 goals, Industry 5.0 is recognized for its human-focused and value-driven approach. The goal of Industry 5.0 is to more efficiently utilize and develop artificial intelligence (AI) and IoT, while enhancing human-machine collaboration in a human-centric manner.

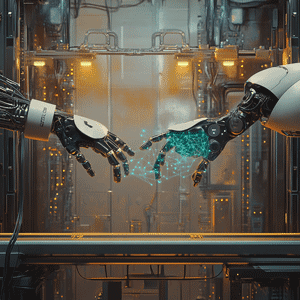
In this evolutionary phase of the industry, it is anticipated that 5D printing, which incorporates five-axis movement into the production process, will merge with AI and IoT technologies, enabling more complex manufacturing processes to be carried out more effectively.
With its ability to deliver structurally robust products and offer design flexibility, 5D printing is expected to gain greater prominence in the future.
The study also focuses separately on the concepts of “3D printing” and “additive manufacturing,” examining their growing research trends in both public and industrial domains. The following chart provides insights into the proliferation, development, and future potential of this technology.
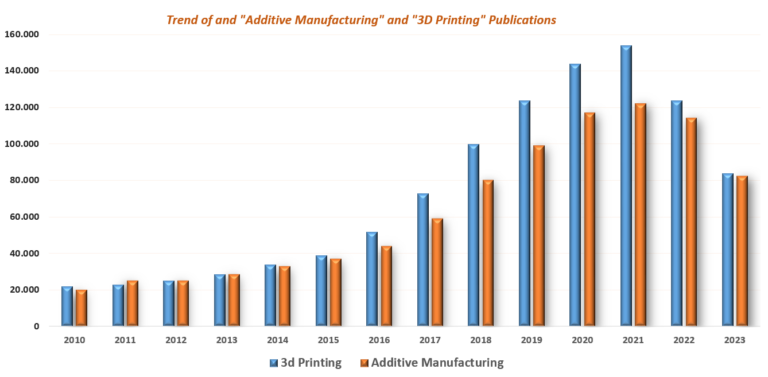
If you’re planning to buy a 3D printer, you can check out our 3D Printer Buying Guide. When buying a 3d printer, you will learn about the criteria you need to consider—such as What to Look for in a 3D Printer. Thanks to this comprehensive guide, you’ll find the answer to the question Which 3D Printer Should I Buy?
Resources to Leverage!
In this section, I’ll briefly introduce some popular websites from around the globe that cover 3D printing libraries, models, events, and competitions. Whether you’re a seasoned professional or just getting started, I highly recommend checking out these sites—they’ll not only broaden your 3D printing horizons but also help guide you toward a higher level of professionalism.
Thingiverse
Think of Thingiverse as the ultimate archive for makers. Here, you can access tens of thousands of free, practical, and popular 3D models and STL files. The platform is welcoming to users of every level—you can explore inspiring designs and even upload your own creations for the community to enjoy!
Printables
Owned by Prusa, Printables stands out with its rapidly expanding library of 3D models. With a variety of events designed to boost community engagement, this site offers you a fun way to gain hands-on experience in 3D printing.
GrabCAD
GrabCAD is home to a vast community where engineers, designers, and manufacturers come together to collaborate on 3D printing projects. It’s a go-to hub for technical and functional projects, offering a wide array of STL files for various components along with diverse software support options.
MyMiniFactory
Tailored specifically for 3D printer enthusiasts, MyMiniFactory is an online platform where users can share and download 3D models. It features both free and paid options and even serves as a venue for designers to earn income from their work.
TurboSquid
TurboSquid is a comprehensive 3D model marketplace that caters to a wide range of industries—from film and gaming to architecture. You’ll find an extensive selection of professional 3D models here, available in both paid and free formats.
Cults3D
This popular marketplace offers a mix of paid and free 3D printable models. Not only can you find a diverse range of designs here, but you can also show your support for your favorite designers by purchasing or downloading their work.
Other Noteworthy Platforms
Don’t forget to check out other excellent online resources such as Sketchfab, YouMagine, Pinshape, Thangs, Yeggi, and Free3D. They’re all great places to dive deeper into the world of 3D printing.
References
- Bănică, C.-F., Sover, A., & Anghel, D.-C. (2024). Printing the future layer by layer: A comprehensive exploration of additive manufacturing in the era of Industry 4.0. Applied Sciences, 14(9919). https://doi.org/10.3390/app14219919
- Mahapatra, R. K., Kaliyath, Y., Shet, N. S. V., Satapathi, G. S., Mahapatro, S. R., & Naidu, M. L. (2024). 3D-printing technology: A review. Proceedings of the Second International Conference on Intelligent Cyber Physical Systems and Internet of Things (ICoICI 2024). IEEE. https://doi.org/10.1109/ICOICI62503.2024.10696498
- ISO/ASTM 52900. (2021). Additive manufacturing—General principles—Fundamentals and vocabulary. ISO Standards. ISO, Geneva, Switzerland.
- Wohlers Report 2015 – A comprehensive analysis of additive manufacturing and 3D printing advancements.