TUM Introduces reAM250: Open-Source Metal 3D Printer Platform
Researchers at the Technical University of Munich (TUM) have rolled out reAM250, an open-source metal 3D printer built to super-charge R&D in additive manufacturing. Announced on 5 December 2024, the project hands labs and start-ups everything—CAD files, firmware, wiring charts—to assemble a full laser powder bed fusion (LPBF) machine on their own turf. By lifting the lid on every design detail, TUM wants to slash R&D costs and speed fresh ideas to market. In short, reAM250 is a research-grade sandbox that anyone can tinker with, free of pay-walled parts or black-box software.
The printer’s 250 × 250 × 250 mm build chamber sits inside a rugged, modular stainless-steel frame—door wide open for interchangeable lasers, scanners and sensors. Need to swap a beam source or bolt on a new vision module? Go for it. The chassis was drawn up to invite upgrades rather than fight them.
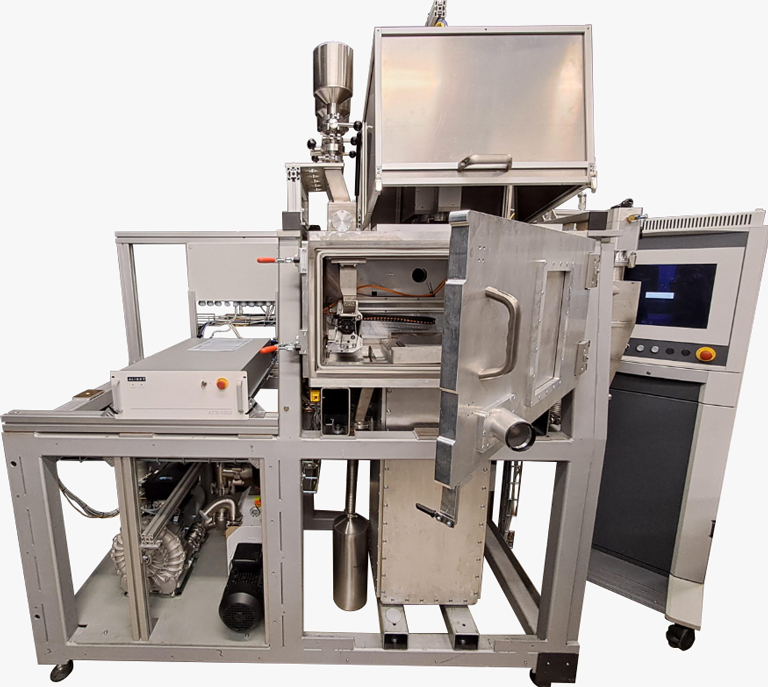
Background
Industrial LPBF has long been corralled behind pricey, closed systems. Adoption has been hamstrung by “part-reproducibility headaches and eye-watering QA costs.” Small labs had two choices: pay the premium or cobble together DIY rigs—both painful. TUM’s answer was to kick those barriers down with “an easily adaptable, self-made platform,” giving researchers a full-scale LPBF machine they can build with standard workshop gear. That way, teams can pour energy into process monitoring, control loops, and new alloys instead of reinventing the hardware wheel.
Technical Specifications
Built almost entirely from off-the-shelf parts, reAM250 is a modular playground: a ready canvas for experimental metal AM. Notable highlights include an inert-gas loop plus a vacuum pump for atmosphere tweaks, a non-contact powder recoater to keep layers pristine, and sensor ports both inline (coaxial) and off-axis for real-time melt-pool or thermal imaging. Because the frame and motion kit are open-architecture, you can bolt on fresh gear as fast as you can dream it up.
Build volume: 250 × 250 × 250 mm
Atmosphere control: Integrated inert-gas flow and vacuum system (argon cycling or full evacuation)
Recoating: Non-contact powder spreading—goodbye layer collisions
Sensors: Ports for coaxial and off-axis monitoring gear
Laser: nLight AFX-1000 fiber laser, seven switchable beam profiles (Gaussian ➜ ring)
Scan head: RAYLASE AM-MODULE-III with SP-ICE 3 controller (~130 µm spot)
Frame: Modular stainless-steel/aluminum skeleton—every bolt documented by TUM
Thanks to the AFX-1000’s shape-shifting beam and RAYLASE’s precise deflection unit, users can stabilize melt pools, tame spatter and probe new scan strategies at will. The vacuum-ready chamber even packs a recirculating gas loop with cyclone filtration—handy for trapping fumes during exotic alloy tests (TUM press kit). Bottom line: reAM250 offers a transparent, tweak-friendly platform for cutting-edge metal LPBF, minus the usual price tag.
Open-Source Metal 3D Printer Platform and Collaboration 🔓
All of reAM250’s blueprints are sitting in plain sight—literally. TUM’s publicly hosted GitHub repo (DavidWenzler/reAM250) bundles everything from CAD files and wiring schematics to firmware and step-by-step docs. Because the university released the lot under a permissive BSD license, even for-profit companies are free to tweak, sell, and scale the design. The same article stresses that the license “encourages industrial reuse, even for proprietary commercial developments.” In other words, a research group can clone the whole setup in-house, no paperwork, no IP red tape—just download, build, and start printing.
Beyond the hardware, the software stack stays just as open. Control duties fall to Autodesk’s Machine Control Framework (AMCF)—an open-source environment tailor-made for additive workflows, again highlighted. Autodesk donated the code so users can map laser paths, run process simulations, and plug directly into motion components. Running on an industrial PLC, AMCF orchestrates every subsystem and bridges popular design tools—Netfabb, Fusion 360, and friends—to the laser and scanner through the 3MF standard, maintaining what is generally referred to as a “continuous data flow from the CAD model to the build platform.
Key industry partners have piled on the hardware muscle. Autodesk handles the control software layer, while laser specialist RAYLASE contributes its scan-controller card and beam-deflection head—gear that lets the open rig rival closed-box precision. B&R Industrial Automation rounds things out with a PLC and Automation Studio HMI to drive actuators and sensors. Put together, the open codebase and pro-grade components create a research workhorse—robust today, future-proof tomorrow. Thanks to a strictly modular layout, advanced users can hot-swap in any compatible laser or scanner without breaking a sweat.
Community Impact 🌍
Throwing the doors wide open on LPBF research, reAM250 hands every lab—big or small—the tools to skip the “build-your-own-machine” slog and jump straight into discovery. Commentators cheer that its fully transparent design “lets institutions share and extend their findings directly,” no hoops required. Rather than burning months on basic hardware, teams can dive into questions that matter: dialling in process parameters, tweaking material properties, or whatever their curiosity flares up.
Need proof? Picture a materials lab downloading the GitHub package on Monday and running alloy trials by Friday, or a process-control group bolting extra sensors onto the gantry to watch melt-pool turbulence in real time. Even corporate R&D departments win: they can pilot new builds on a low-risk reAM250 rig instead of jeopardizing their certified production lines. Because the platform sits under a permissive BSD licence, a firm is free to slot in its own closed-source control code—no lawyerly headaches—3D Printing Industry confirms.
Many see the project as metal AM’s answer to the RepRap revolution. Open-source printers like Prusa reshaped the desktop scene; reAM250 aims to do the same for powder beds. Crucially, that BSD badge means improvements flow both ways: academics can publish fresh sensor hacks or algorithms, while companies can fold open modules into commercial products. TUM’s iwb institute has already waved collaborators in, noting it is “open to partnerships that tap the platform’s potential” (mec.ed.tum.de). With every schematic parked on GitHub, contributors worldwide can fork, remix, and push back. Bottom line: reAM250 is on track to become the go-to research-grade 3D printing platform for metal, flattening entry barriers from campus labs to factory floors.
What’s Next 🚀
With the reAM250 blueprints now out in the wild, the ball is squarely in the community’s court. TUM’s engineers have already stress-tested the rig by printing benchmark parts, proving the concept holds water (mec.ed.tum.de). From here on, they’re counting on makers, researchers, and industrial tinkerers to bend and stretch the platform in directions they haven’t even imagined.
What might that look like? Think supersized build chambers, swap-in laser sources, smarter powder-handling modules, or plug-and-play sensor packs for real-time melt-pool sleuthing. Because the skeleton is modular, a team could just as easily pivot the frame toward metal binder-jetting or a hybrid tool-path experiment. TUM will keep the GitHub repo groomed, but most of the magic will happen in forks and pull requests scattered across the globe—exactly how open hardware should grow.
If that hive mind kicks into gear, reAM250 could evolve at break-neck speed: one lab refines the scanning algorithm, another bolts on an infrared eye, a third polishes the UX until Grandma can queue a print. Piece by piece, the machine could cement itself as the go-to R&D workhorse for metal AM. As TUM likes to remind everyone, stripping away pricey black-box constraints is the fastest way to push metal 3D printing further than we’ve ever taken it. Ready to dive in?